Companies asked for integrated supply chain planning. They got it. It does not work so well. Now what?
Sharing A Story
Last week, I met a client for breakfast in Frankfurt. Let’s call her Sally. As a leader of a global supply chain organization, her goal was simple. She was trying to define and drive supply chain excellence. In the last year, she worked with three consulting companies. Each recommended a supply chain planning system tightly integrated to Enterprise Resource Planning (ERP) along with collaborative planning with sales in Sales and Operations Planning (S&OP). Sally followed the advice to the letter; yet was struggling with how to drive improvement.
Her focus was on technology implementation. Not process improvement. Things were not working very well. The business was growing. Demand error was increasing. As the business flexed, she felt trapped. Her processes could not adapt to the changes in the business. Collaborative sales input planning added 15% and 21% bias, and she had never thought about testing the engines in demand and supply planning to see if the solutions were giving a beneficial plan.
In short, she believed that she needed integrated planning. The company agreed to move forward. When completed, she felt confined. The solution was too rigid; yet, she had never tested the output.
I find that this is the case for many clients. As shown in Figure 1, today’s processes are controlled but lack agility. Most are reactive, traditional and cautious. Why is this? We got what we asked for. Most clients designed planning systems with tight coupling of planning to ERP without stepping back and asking the question, “What Does Integrated Planning Mean?”
In contrast, agility is the output of systems design. In contrast, the design of ERP-based systems is functional efficiency. Most learn the hard way that functional efficiency and alignment are geometrically in opposition. The solutions optimize source, make and deliver within silos, but lack the ability to drive alignment and improve agility. Consequently, we are making our systems more efficient, but less effective.
When it comes to agility, there is no common industry definition. As a result, many people tout the need to improve agility but are unable to deliver because of a clear definition. This was the case for Sally. She had taken the consultants recommendation on blind trust and never thought about the ‘philosophy’ of the systems implemented. Likewise, while she wanted and desired agility, the organization lacked a good definition. She had not mapped demand flows or studied the impact of network design strategies.
Figure 1. Current Supply Chain Attributes
Starting with a Definition
In our research, we define agility as the ability to have the same cost, quality and customer service given a level of demand and supply volatility. The first step in the delivery of an agile supply chain is a clear definition.
The second step to drive value is defining the flows and aligning the tactics. The agilest supply chains are outside-in using channel data. This decreases demand latency and improves market sensing. The traditional supply chain process with a focus on orders and shipments as a source of demand (transactional efficiency) is like dancing on a back foot with your hands tied behind your back.
While often reducing demand error is not possible, companies can design the supply chain to increase in agility. This includes postponement, common platforms, product formula simplification, alternate sourcing, and buffer strategies. To accomplish this requires a strong capability on network design. Companies with a strong center of excellence and clear definition of supply chain excellence do this best. Unfortunately, the companies that have accomplished this feat are about 7%.
Companies, like Sally, want to change, and many are searching for answers. Consultants flood the market. I find many giving bad advice. Their focus is on implementing technology versus delivering business results (many make money through kickbacks selling Enterprise Resource Planning (ERP) solution platforms). Buyer beware.
Why Does This Matter?
As shown in Figure 2, the future and desired state in the next five years is much different from what we have today. Companies want more than functional silo optimization and a reactive response. The goal is agility, proactive and outside-in. It is for this reason, that we must abandon the thinking of silo-based optimization of ERP and conventional Advanced Planning solutions. Instead, start with network design. Build agility into the supply chain using tactics to buffer demand and supply and align push-pull decoupling points. Use this data as the targets for your cognitive and prescriptive analytics. These solutions based on machine learning and cognitive computing are evolving fast in the market and ever so slowly in the labs of the conventional ERP providers. Define ERP as only the financial system of record for transactions. To drive agility, test multiple systems and implement best-of-breed solutions that give the best answers. Test and learn with technologists. Side-step big projects and large consulting groups.
Figure 2. Business Leader Goals for Five Years
I hope this helps. Five years are not very far away. To achieve the needed shifts, companies need to get started today. So, when companies ask me about the implementation of technologies like SAP IBP on HANA, I ask “Why?” I think that we need a shift, not more of the same.
Let me know your thoughts. I look forward to hearing from you.
Help Us with Research?
If you like our research, please consider helping us finish some of our studies. We currently have a quantitative project in the field on Satisfaction with Supply Chain Planning. Our philosophy is, “You give to us, and we give to you.” When business leaders take our surveys we share the responses openly. Our research is independent and open. So, if you are a business user and have knowledge of supply chain planning, we would love to have you participate in our study. We are closing this study next week.
Join Our Event to Act Differently and Drive New Outcomes
This week, I sent personal invites to business leaders and Supply Chains to Admire Award Winners to attend the Supply Chain Insights Global Summit on September 4-7, 2018 in Philadelphia, PA. The registrations are rolling in. We expect it to sell out.
Designed to help supply chain leaders think differently and to drive new outcomes, the agenda is unique. Designed for extreme networking, the conference is small and intimate. Where else can you attend a conference with no sponsors, a 60/40 ratio of business users to technologists, and hand-picked presentations with a focus on driving change? Meet technology innovators and network with others. There are twenty seats left. Don’t let this opportunity slip you by.
For additional reading on integrated planning check-out these blogs.
Is Integrated Planning Rubbish?
Was Integrated Planning a Hoax?
Reflections on Integrated Planning
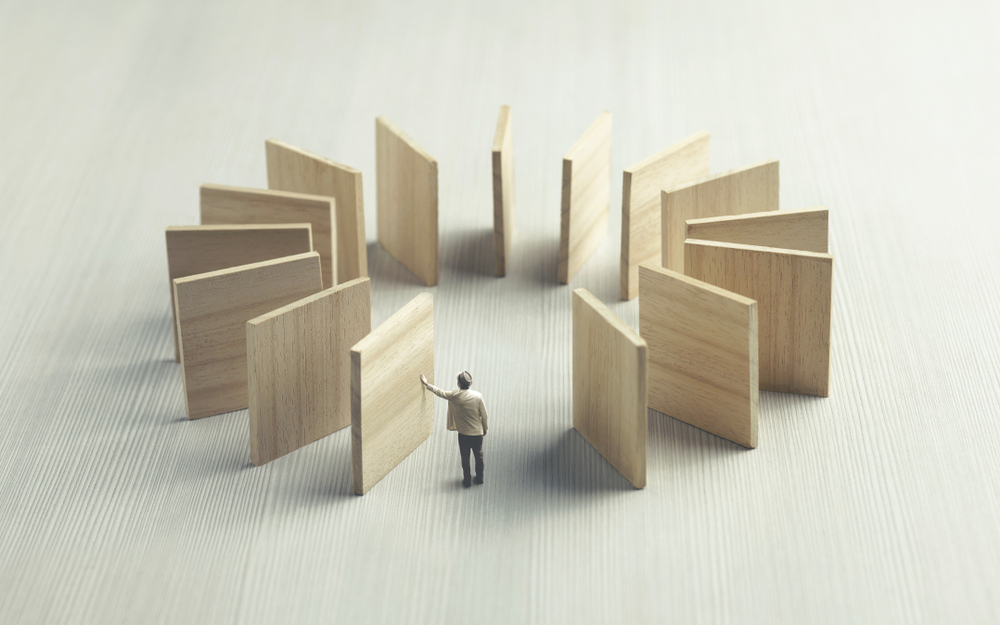
Please Don’t AI Stupid
Drip. Drip. Drip. Industry 4.0. DripBig Data. Drip.The Connected Supply Chain. DripDigital Supply Chain. Drip.Autonomous Supply Chain Planning. Drip. Self-Healing Supply Chains. Drip. Touchless Supply