Today, my LinkedIn newsfeed fills with smiling pictures of supply chain technology leaders celebrating their times at the Gartner Supply Chain Planning conference in England. Birds of a feather flock together. As my reader knows, I wear a cloak of different feathers.
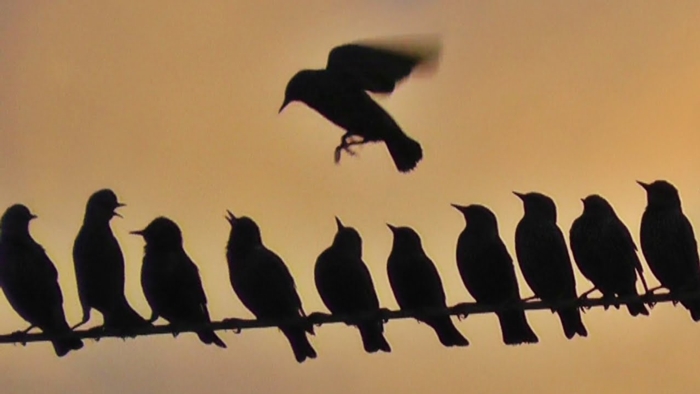
When companies ask me, “Will I see you at the Gartner conference?” I laugh.
I think I am the only person in the supply chain space who has been disinvited to a Gartner event five times. I take it as a badge of honor. So, no, you will not see me at the Gartner event, and I am also not a puppet to parrot the Gartner gospel. Although many of the frameworks I built, like the one on S&OP, are still used. A second badge of honor, I think.
I think that the Gartner engine creates Groupthink. I know the “beat” well. I lived it. I was a Gartner analyst for two years in the period of 2000-2002 and an AMR Analyst for the period of 2005-2010. I left Gartner because I was tired of speaking to the late adopter about technology, and I left a second time when Gartner bought AMR Research. I just have to believe in what I am doing.
There are no sour grapes here; Gartner’s conferences are great for networking. I just don’t think the business model serves the industry well. The model preserves the status quo. Which is fine if the current state is adding value. But what if it is not? This is the focus of this blog.
The Litmus Test
The goal of a technologist is to garner some Gartner ink for their website. In the process, no one asks, “Are we solving the right problem? Or are our solutions making a difference?” As a geeky gal, I think a lot about planning technology and sustained outcomes. I question if we are meeting the goals of helping companies make better decisions. My litmus test is the balance sheet. My moment of truth is, “Did the company, over time, outperform competitors on the key metrics of margin, inventory turns, growth, and Return on Invested Capital (ROIC).
For those interested, only 27% of companies listed on five planning technology companies’ websites beat their competitor’s performance at the intersection of operating margin and inventory turns for the period of 2010-2022.
For laughs, grins, and giggles, pour a cup of coffee and take a look yourself. Cruise the websites. Many companies are on multiple websites. One company has no named case studies listed on its website and hosts events with many “former executive speakers.” Laughable right? Don’t be naive. These advisory councils are paid actors as a part of an executive council to drive leads.
Today, manufacturing companies hold 28 more days of inventory than in 2010, and in eight out of nine companies that I visit, the Forecast Value Added Analysis (FVA) is negative. I seldom see a well-deployed supply chain planning project meeting driving insights. One company that I work with mentioned that they have 1700 employees with “data” in their titles, but they have no insights. Another company that I work with had 200 planners in 2002, 400 in 2007, 700 in 2012, and 1400 today. We are burning human potential and doing a poor job of implementing the technologies.
Why do companies not hold themselves accountable for driving better and sustained results? This is my question and the focus of this post.
Are We Driving Value Today? Sadly, I Don’t Think So.
The issue lies in the word “project.” Most of the deployments are just that. They are projects. Seldom do companies use technologies to make better decisions in a disciplined process where the company knows:
- Did the solution produce a good plan?
- How did we perform to the plan?
- What needs to happen to improve balance sheet outcomes?
- What defines supply chain excellence? How do we balance risk and opportunity?
As a side note, supply chain planning should never be about the speed of implementation. Ironically, the projects I followed with the best results were often long and focused on building human potential. These successful implementations were driven internally and focused on using technology to drive better decisions. (As a side note, I know of no consultant that does supply chain planning well. I recommend a few boutique shops in Europe, but this is for a blog post for a later day.) In the process, do not confuse improving functional metrics on a local project as sustainable, long-term business results.
While the concepts of Artificial Intelligence(AI) are popular. While promising, unless we are clear on the problem, no technology, including AI, will be effective. As ideas roll around in my head, I am becoming more and more convinced that the current definition of supply chain planning is not aligned to drive the level of supply chain performance improvement that companies need.
How Do We Shift Focus?
Let’s start with a discussion on solving problems. As I cruised the web from my hotel in Houston, I found some quotes that I love:
1.“We cannot solve our problems with the same thinking we used when we created them.” – Albert Einstein
Agreed. Supply chain planning, as we know it today, was defined in the 1980s when the supply chain was regional and localized. The current definition of planning does not serve the global organization well. The reason? The organization has become more functional, and the focus on IT standardization improves transactional efficiency but not flow. Focusing on transactions and integration blinds the supply chain leader to flow opportunities and variability challenges. While the graph offers great promise to visualize and manage flow while improving predictive analytics, the current graph technologists are chasing RFPs and taking pictures at Gartner conferences.
2. “Sometimes problems don’t require a solution to solve them; Instead, they require maturity to outgrow them.” – Steve Maraboli
We must learn from the past, to unlearn, and rethink how to improve outcomes. How does the industry the maturity to outgrow their current solutions? The current definition of supply chain planning no longer solves the problem for a global supply chain.
3. “It isn’t that they cannot find the solution. It is that they cannot see the problem.” – G.K Chesterton
I find so many leaders do not understand the workflows of supply chain planning. As an FYI, we do not have end-to-end planning. My point of view? Anyone who says that they are implementing end-to-end planning doesn’t understand the application. So, let’s not play games. Don’t fool yourself and your organization. The workflows of sourcing and logistics are not connected to traditional supply chain planning. The constraints and issues of procurement and logistics have grown exponentially over the last decade. The traditional focus of Supply Chain planning is on managing manufacturing constraints. In traditional applications, the flows are linear, not bi-directional. Demand is consumed: variability is not managed. Many “leaders” wave their hands and discuss techniques—probabilistic planning, control towers (that do not control), Demand-Driven Materials Requirements Planning (DDMRP) (which is anything but demand-driven planning),– but we are not talking about the redesign of work to improve outcomes. This is the discussion that I think we need to have, but we must first ground ourselves in the problem that we need to solve.
4. “We fail more often because we solve the wrong problem than because we get the wrong solution to the right problem.” – Russell L. Ackoff
This is today’s issue. As it is currently defined, supply chain planning solves the wrong problem. The goal should be improving balance sheets to drive outcomes and improve organizational alignment. This is not the case today. Current solutions improve functional outcomes for a project, function, or local region.
The right solution provides insights through managing flows from the customer’s customer to the supplier’s supplier bi-directionally. The current fascination with transactions and tight integration to the budget limits the potential. The primary user should be the business leader, not the planner. Today, the focus is on improving insights for the planner. Localized optimi and technologies for isolated groups, called planners, are insufficient.
5. “Solving problems means listening.” – Richard Branson
Listening and learning are essential to drive new outcomes. I recently posted a LinkedIn article on the gap in our personal and work lives on technology usage. The pace of automation in our personal lives is mind-numbing. In contrast, not a lot has changed in our business lives. We still know more about the pizza delivery for lunch than the timing of the inbound truck to a plant (the biggest gap in visibility is an inbound ETA). Our supply chains are surrounded by data—unstructured, image, and streaming data– that is largely unused. We speak of real-time decisions but do not know how to use channel data to decrease demand latency effectively.
We Are Wasting Talent. Meet Brandon.
Which brings me to the story of Brandon.
Imagine a lazy Sunday morning at a diner. I rushed from the house late and had what seemed to be a million things to do, but I had agreed to meet a friend’s family at a diner before finishing an endless number of Sunday chores.
After brief introductions and some coloring with my friend’s grandson, I settled into my chair to begin my Sunday love fest with black coffee. Savoring the sips in a ceramic mug, I glanced at the menu. In the process of trying to decide between the pancakes and biscuits (a tough choice with minimal coffee), Brandon (who I don’t know at this point) peppers me with a question mid-sip, “So, Mark tells me you know a bit about supply chains.”
I laugh quickly, thinking about how to side-step this question. I hate boring folks with supply chain info. My relationship with supply chain content is intense. I don’t know how it happened, but studying supply chains and helping people is my stick. My best friend tells me that I fell down the supply chain hole—a rabbit hole of sorts– and that my thinking is so structurally encased with deep supply chain thoughts that the average person finds it boring. I did not want to bore Brandon, and I respect Mark, so I looked up from my menu and replied, “Yes, a bit. Why do you ask?”
He replies, “I majored in communications and recently took a position at a manufacturing plant helping to manage inbound raw materials. I don’t know anything about supply chain and wonder how to do it better.” Brandon continues to tell me about his job. I wince when he tells me about the manual hourly data dumps out of SAP into Power BI to rationalize manufacturing material requirements and allocate tight supply between the many manufacturing plants he serves. The poor boy spends most of his day in meetings and fighting fires. He then states, “I am sure there is a better way to do this; I would love to know what you think.”
I smile. Here is a twenty-six-year-old and an eager new hire struggling to manage inbound supply. He has had no training in SAP on material flow or supply chain in general. Brandon is managing material flow by brute force. There are more insights about the delivery from Doordash on his pizza delivery for lunch than his inbound factory supply.
He does not know that he rides the bullwhip every day or that there are no good solutions to manage plant supply to help him. (While Lean DNA and Source Day are advancing insights from a supplier perspective, they are not a good fit for this process manufacturing problem full of the nuances of swaps, grades, and yields.) And, if the solutions existed, his financially-driven organization probably not invest.
Brandon is a gamer. He loves technology. In his personal world, he is the epitome of a digital native. In his business world, his day is full of meetings and non-sensical data pulls. Getting data and insights is tough and out of step with the pace of business.
He works at a company that has never designed their supply chain. The organization invested in ERP but currently lacks a holistic understanding of planning. The Company is a local medium manufacturer with thirteen manufacturing facilities managed by a financial team focused on making a leveraged buyout work.
As the plate of biscuits arrived, I thought about the plight of the Brandon(s) of the world and how we are wasting much of the talent of the digital natives in current supply chain organizations. Current forecasts project that we will be short 40-20% of the required talent needed in the supply chain by 2030. The Brandons of the world will become data jockey slaves to current ineffective systems when we could solve the bigger problems.
I also reflected on how most technologists I work with focus on solving the wrong problem. Most of my friends are having the wrong discussions. Few have walked the plant floor to see that the most used technology is the humble Excel spreadsheet that will never be equal to solving supply chain planning needs. Most of my friends are birds of a feather flocking together in a lucrative world that lost its way.
The supply chain is a complex, non-linear system. Managing the supply chain is analogous to gaming in the real world. A smart company would ask every gamer and musician on their team to volunteer to be part of a new team to redefine supply chain capabilities. Gamers understand simulation and non-linearity, while musicians revel in the world of synchronization and harmonization. They would shun convention and use network design tools to show executive teams how tight integration of the linear math of finance cannot and should not directly integrate with the complex, non-linear world of the supply chain. Financial transactional data is only one of many inputs.
These new teams would measure and reduce the bullwhip. The team would model the impact of demand latency and the shifts in demand and market drivers, knowing that the order is a poor proxy for demand. The new team would measure the carbon impact of their network and actively manage the environmental impact. Using new approaches, they would continually educate their executive teams to manage risk while embracing opportunity. The gaming mindset would plot the dead-end journey of the organization managing through functional metrics inside-out and educate leaders to the promise of the organization managing via a balanced scorecard outside-in.
Wrap-up
That is my magic wand. Until then, I will continue to delete the many pictures of happy faces in front of a booth (that sadly looks like all of the others) at events like the Gartner planning session that will never serve the Brandon (s) of the world. Instead, the feathers will only line the pockets of venture capitalists, technology sales teams, and event companies. Birds of a feather will flock together as we waste much of the potential of the digital native.
Look at yourself in the mirror and ask yourself how supply chain planning can help. What is the problem that needs to be solved? What do you need to unlearn?