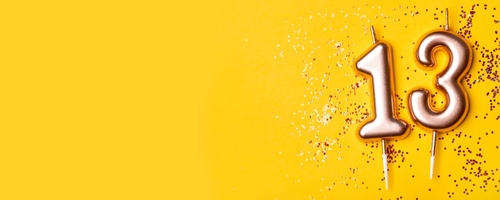
Thirteen years. 600 posts. Where does time go?
For over a decade, since founding Supply Chain Insights in 2012, I have pounded the keyboard, asking business leaders to think more holistically about the impact of supply chain decisions on the firm’s value, the improvement of a value chain, and the impact on the environment. If written today, my gravestone would read, “Here lies Lora. A failed blogger.” Help me to change this projectory.
Change is Hard. Unlearning is Tougher.
Despite the evolution of technology, none of the 28 industry segments I follow can drive improvement at the intersection of operating margin and inventory turns. While many might see the issue as change management, I think that the journey must start with unlearning.
The industry is full of experts. Guess what? The expert opinion is not equal to the challenge. We must unlearn before we can drive change. The answer lies in the shifting of traditional paradigms.
The reason? I think that the answer has five parts:
- The Belief that the Industry Has Best Practices. That tightly integrated advanced planning (APS) coupled to Enterprise Resource Planning (ERP) using order data is sufficient. Over the past decades the definition of the supply chain has become narrower with a focus on supply and improving enterprise efficiency which decreases resiliency.
- Investment in Legacy Technologies. The industry continues to invest in technology architectures that are inside-out and limited. This includes the evolution of schema-on-read architectures and the use of advanced sensing and network automation as companies work through endless cycles of legacy technology like ERP and APS.
- Functional Metrics and the Lack of Alignment to Strategy. Process-based companies continue to focus on manufacturing efficiency (OEE) and discrete on procurement (PPV) without designing the supply chain to balance transportation, manufacturing, and procurement to a balanced scorecard.
- The Lovefest with Shiny Objects. This year, the shiny object is AI (artificial intelligence) and touchless systems. Last year, the lovefest was digital supply chain transformation. The issue is that most companies are using new forms of technology to make bad decisions faster. The reason? The industry is not clear on desired outcomes.
- Clarity on Value. Few companies are clear on the number of supply chains they operate, design the rhythms and cycles of each, and align metrics to the strategy. Most focus on cost reduction, assuming that functional cost translates to operating margin. Guess what? It doesn’t. The supply chain is a complex, non-linear system requiring trade-offs that need to be designed.
Retrospective
Let’s start with a focus on process-based industry value chains heavily influenced by the price of oil. Note the fall in 2014-2019. Each of the process segments translated the shifting cost to improved margins. However, no process industry was resilient through the recession. While many risk management experts might say this is due to supply risk management, I think the issues are more insidious. I believe that the most significant risk to the supply chain is outdated demand management practices and the inability to drive bi-directional orchestration to pull the right levers to balance the process of transportation, procurement, and manufacturing in concert.
Figure 1. Price of Crude Over Time
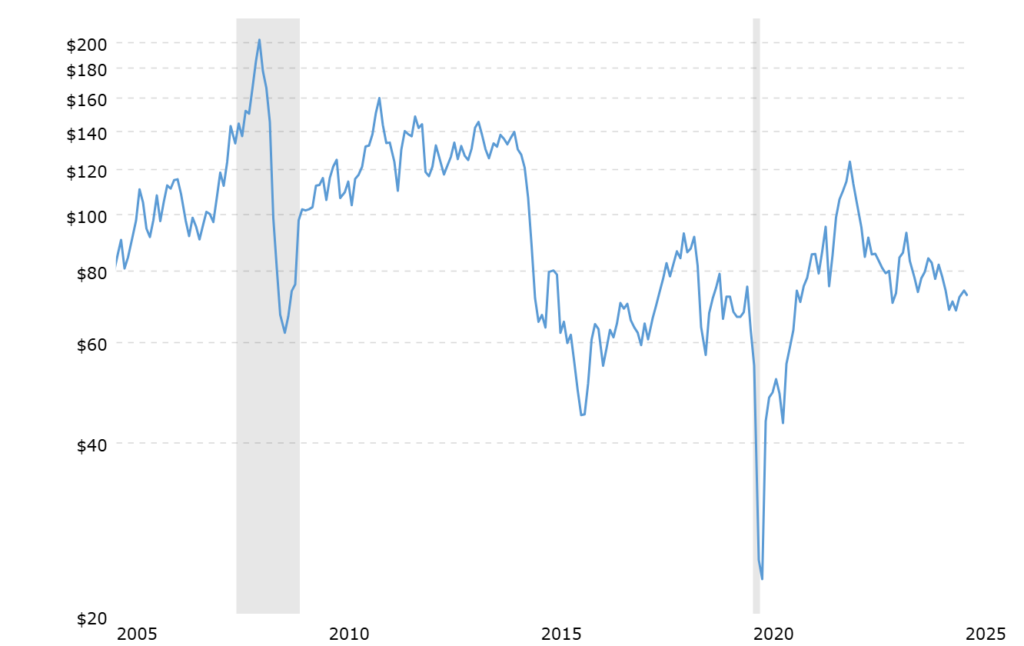
Most industry professionals use terms like VUCA and express concern over variability in the past decade. Figure 2 shows that actual variability was low before the pandemic. Most companies allowed corporate politics—focusing on long planning cycles that did not improve Forecast Value Added or supply feasibility—to degrade margin opportunities.
Figure 2. Global Supply Chain Index Over Time

A Critical Look at Industry Performance
Notice in Figures A-C that the beverage, chemical, and containers/packaging industries took advantage of the lower cost of crude oil but failed to build industry resilience. They struggled to regain margin in the pandemic despite the very low cost of fuel in 2019-2020. The average company in the pandemic took eight months to align its organization to shifts in demand and rethink supply strategies.
Figure A: Beverage Industry Aggregate Industry Trend 2014-2023
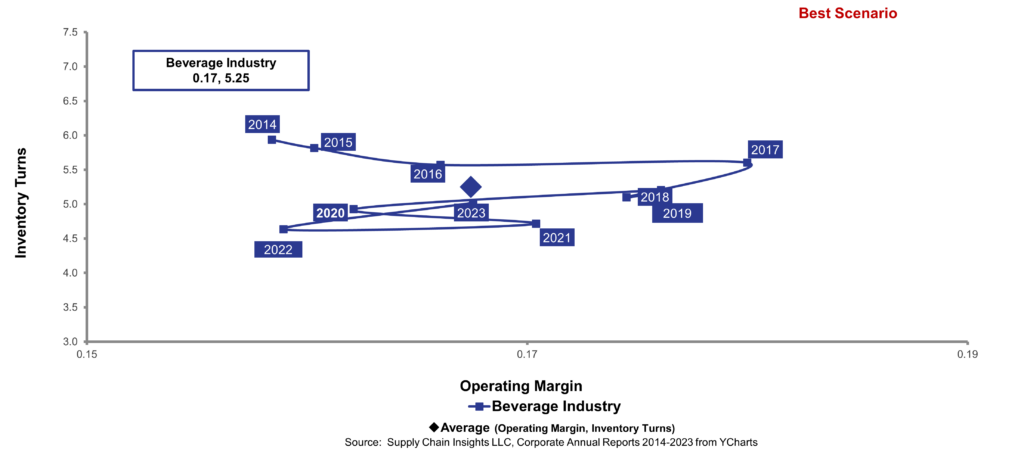
Figure B. Chemical Industry Aggregate Trend for the Period of 2014-2023
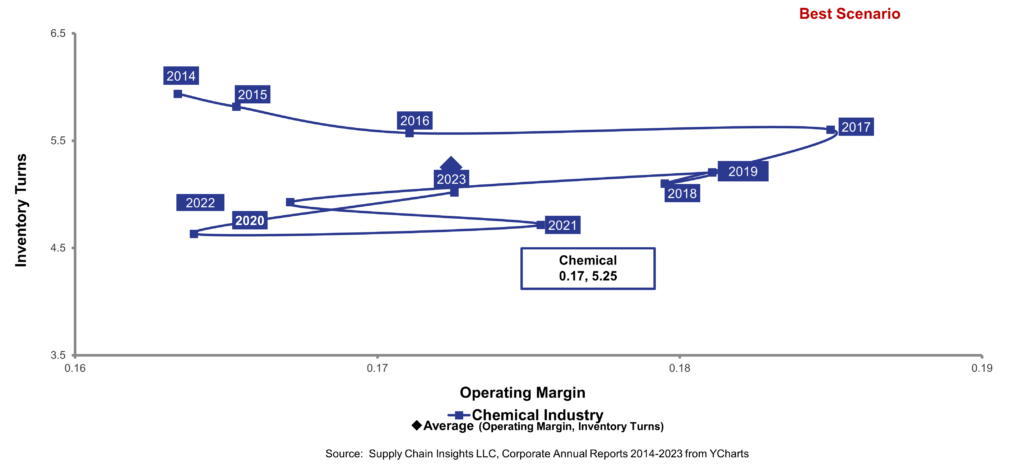
Figure C. Aggregate Trend Containers and Packaging
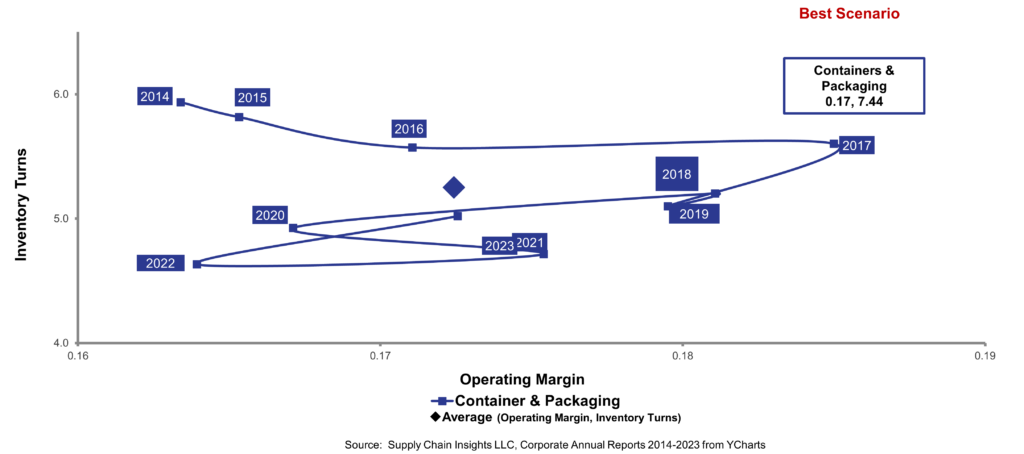
In a similar pattern, the apparel industry, which is very sensitive to the cost of labor, lost margin and struggled to regain resiliency during the pandemic.
Figure D. Aggregate Industry Trend Apparel Industry
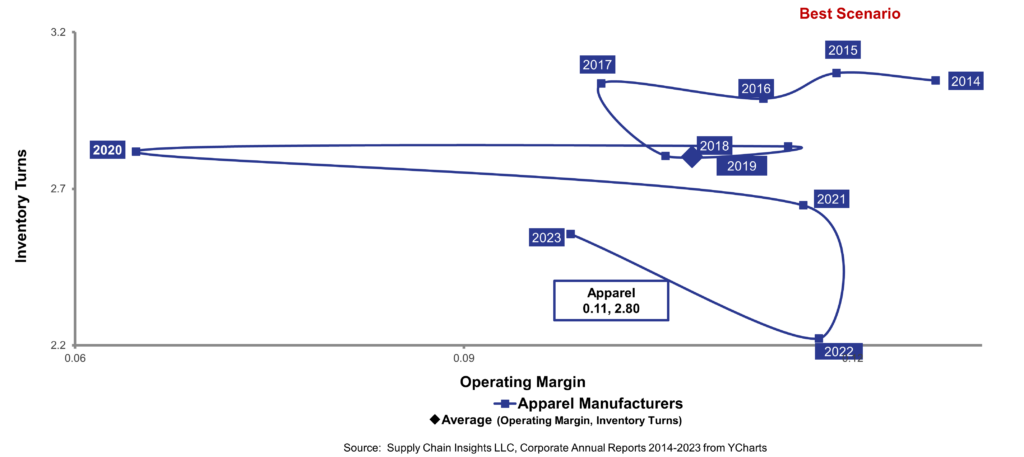
Groupthink
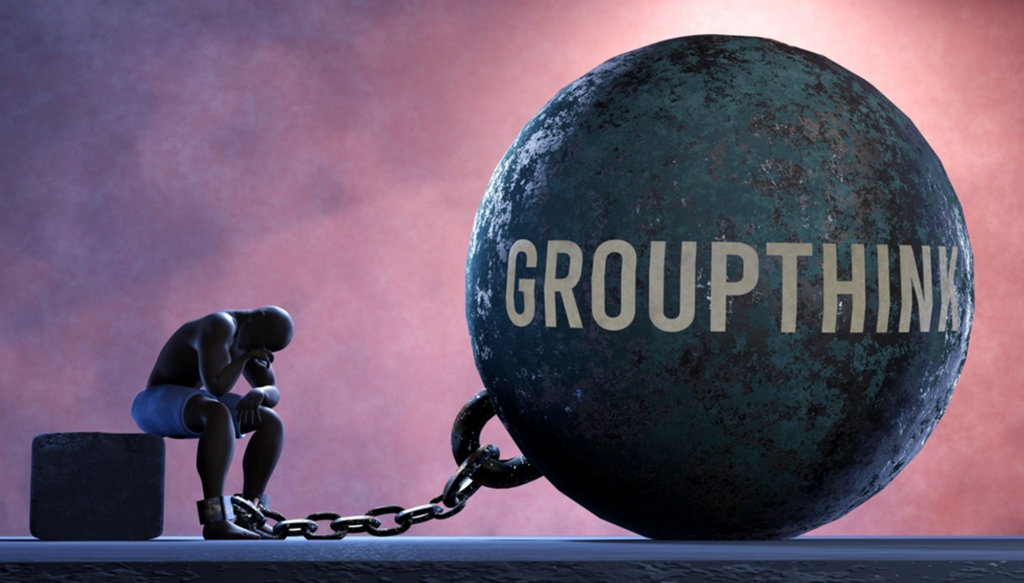
In short, the industry struggles with Groupthink. In our research, small regional companies outperform large multinationals. (The time to adjust to market shifts is much longer in the global multi-national.) The industry is full of “experts” with gold cufflinks sharing what they believe is sage advice, but industry progress does not change.
Start your journey by defining supply chain excellence.
I define supply chain excellence as the ability to outperform an industry peer group during a time period. In the Supply Chains to Admire Analysis, I apply three measurements–improvement, resiliency, and balance to the patterns in the orbit charts. The premise is that best-performing companies outperform their peer group (improvement) with a tight pattern (resiliency), while balancing operating and capital expenses.
We paused publishing the report this year while we worked with Georgia Tech on the right balance of metrics to drive market capitalization/employee. These two reports are coming soon. I will be writing insights throughout the three- to four-week process.
In short, fight groupthink, don’t chase shiny objects, and avoid the endless upgrade cycles of legacy technology. Be open to rethinking processes outside-in to improve the organization’s ability to sense and respond.