In manufacturing-based companies, 70-80% of costs are in the processes of source, make and deliver. Labor is an important input with 50-60% of company employees reporting through supply chain organizations.
Is talent a cost or an asset? Most companies say employees are an asset, but treat it as a cost. Today, with companies having a keen-focus on costs, talent development often takes a back seat. In this post I argue that it needs rethinking as an important asset.
Background
Supply chain processes are relatively new. The processes are evolving. While the practices of finance are over 200-years old, in contrast, supply chain management as a cross-functional practice (the combination of make, source and deliver) was recently defined in 1982. There is a belief that investments in technology, processes and talent improves balance sheet results and organizational agility. Our observation is that while projects drive pockets of improvement, it is difficult for the supply chain team to impact the balance sheet.
What defines supply chain excellence? In a recent study, our goal was to understand the impact of process and technology choices on balance sheet performance. We analyzed the impact of 150 factors on 493 financial metrics for the period of 2004-2016. This included responses to 3604 questions by 1063 individual respondents, in 40 studies, representing 756 unique companies.
This research was tough work. It took us four months. The results? There is no correlation between technology choices and balance sheet results. Despite all the ads at airports and pretty PowerPoints by consultants, we cannot find support for the claims of “Best Run Companies Use Technology X” or “Manufacturing Companies Using Consulting Services With Company Y Have Better Results,” or a single instance of Enterprise Resource Planning (ERP) drives better results. Across the industry, we find that companies think they are managing costs and inventory better through technology investments like supply chain planning, but they have a false sense of accomplishment. Does this mean throwing out the baby with the bath water? No. The goal should be ensuring that projects drive long-term balance sheet results.
By graphing the financial metrics through orbit charts, we find that 90% of companies are stuck at the intersection of operating margin and inventory turns. With rising complexity, most companies are unable to make improvements in a balanced scorecard.
What made a difference in outperforming the competition in costs? The answer is simple. Empowered talent. As shown in Figure 1, we find companies managing talent better than their peer group have a cost advantage.
Figure 1. Results of Analysis
So what are the characteristics of companies managing talent better than their peer group? What are the gaps to close? There are six: belief in the company; appreciation for work; the need to be a part of a talented team; admiration for leadership; training and professional development; and flexible work schedules. Empowered workers make a difference. With the flurry of M&A, industry consolidation, outsourcing, and downsizing, the gaps for North American manufacturers are increasing.
Figure 2. Talent Gaps
Closing the Gaps
Overall, 69% of supply chain professionals are satisfied. Baby boomers are happier than Gen X or Millennials. Employees working for technology providers or academics are more satisfied than employees working for manufacturers. This is a warning for manufacturing companies. The gap is significant, and we believe growing.
More insular companies–those that do not encourage networking, training, professional experiences–tend to score lower on employee satisfaction. So, if you are working on improving supply chain employees’ satisfaction, consider the elements on the word cloud from the surveys open-ended responses.
Figure 3. Word Cloud of Open-Ended Responses
Most companies have an endless cycle of cost cutting. This is especially true in the last two quarters of the year.
Cost cutting is more severe in the back office than the front office teams of sales and marketing. Companies are often so busy pinching pennies that they miss the greater opportunity. With slowing growth, as companies end the year, many teams face draconian cost-cutting efforts. When faced with these choices, just remember that empowered employees make a difference. Supply chain talent matters.
How Do You Measure Up? How Can We Work Together to Build Teams?
We want to help. Find out how your organization stacks up. Due to popular demand, we are kicking off an organizational benchmarking effort. In this work, companies can use the baseline data from a recent survey of over 600 respondents to understand the relative satisfaction of their teams by generation and role. Our goal is to have companies participating in this benchmarking study to share insights with each other in a networking session, i.e. in a facilitated share group in January 2018. As with all of our research, the responses for this work are held in confidence and never shared publicly. Let us know your interest.
In addition, we are opening registration for the January Cross-Company Cohort on Next-Generation Supply Chain Processes. These online courses are designed for senior managers and directors. The goal is use research, case studies, videos and collaborative discussions to help supply chain teams learn next-generation concepts. With multiple companies in the course, the group learns from each other. Each company can register up to two leaders per cohort. Each class goes through seven modules. There are cohorts in the Americas, Europe and Asia. Let us know your interest.
Share the presentations from the Supply Chain Insights Global Summit with your team. They are now posted, both the videos and PowerPoint presentations, on the Supply Chain Insights Global Summit website. We believe in open content. Use the presentations to help your organization learn and imagine the future. We remain committed to helping teams evolve by bringing the best forward-thinking case studies in the industry, and then following up through the sharing of open content. We want to build a guiding coalition to rethink supply chain processes and prepare organizations for Supply Chain 2030. Based on attendee feedback, we have revamped the summit to exclude sponsorships in 2018. As a result, the 2018 Summit will be smaller and more intimate, but with a focus on business leaders. There will be no technology sales personnel or market teams at the 2018 Summit in Philadelphia, PA. Mark your calendars for September 4-7, 2018. We hope to see you there.
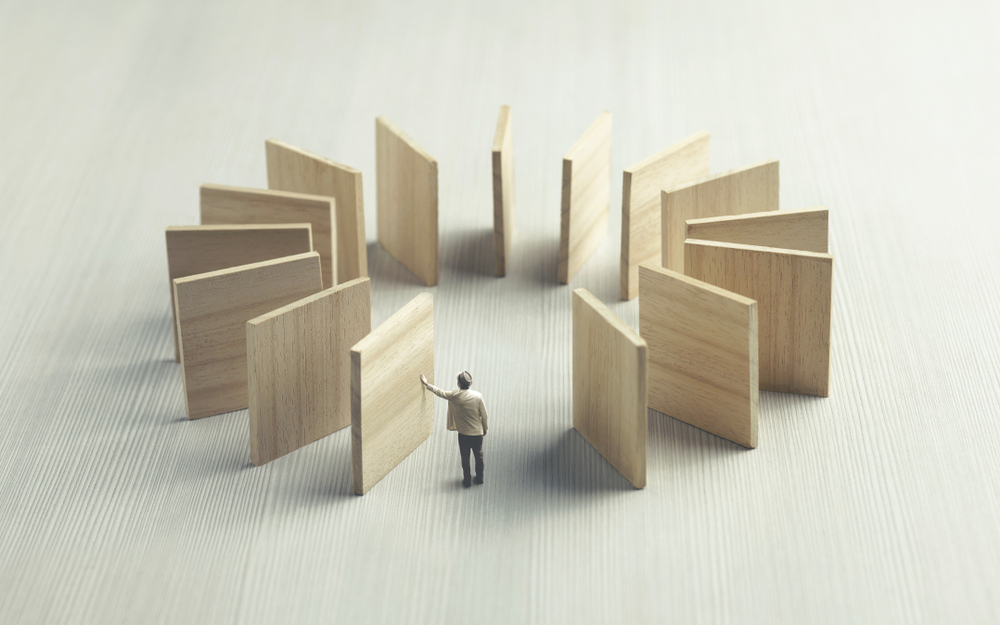
Please Don’t AI Stupid
Drip. Drip. Drip. Industry 4.0. DripBig Data. Drip.The Connected Supply Chain. DripDigital Supply Chain. Drip.Autonomous Supply Chain Planning. Drip. Self-Healing Supply Chains. Drip. Touchless Supply