In the United States, families are packing for Labor Day. The exodus from the cities leads to jammed roads and packed parks. Now a ritual, Labor Day is the first Monday in September. Dedicated to the social and economic achievements of American workers, it is a welcome three-day weekend. So, with labor day approaching, I am penning a blog on supply chain talent.
Labor day also signals the end of summer, and for many supply chain leaders the beginning of 2017 strategy discussions and intense S&OP debates to finalize Q3 and Q4 planning. Slow growth and rising costs dominate meeting agendas.
In strategy development, the missing link for most supply chain leaders in the Race for Supply Chain Excellence is developing and retaining supply chain talent. While most have programs for entry-level hires and executive leaders, as shown in Figure 1, the biggest gap is in the development and retention of mid-management leaders (senior managers and directors).
The reasons are many: early retirements, growth in global markets, and the growing importance of supply chain leadership. The struggle is what to do. What defines success to fill this gap? Certification programs focused on historic practices are not sufficient, and the current academic programs are a better fit to build entry-level skills.
Figure 1. Supply Chain Talent Shortage
Getting clear is the first step in building supply chain talent. As shown in Figure 2, traditional supply chain thinking (functional orientation and a project-based focus) and the lack of organizational alignment are major barriers. Before I started doing this research, I believed procurement and manufacturing were aligned. I thought the primary issues were between commercial teams and operations. I was wrong. While this is the case in 50% of the organizations, there are many organizations with large alignment gaps between finance/operations and procurement/manufacturing. Executing a strategy requires closing these gaps.
Building next-generation supply chain processes to drive higher levels of value also requires questioning the status quo and rethinking processes. The focus cannot be about only continuous improvement of existing processes. Customer-centric, demand-driven, network of networks, and outside-in processes will become the reality in 2030. The supply chain of the future is no longer about cost containment. Instead, it is the engine of growth through test-and-learn capabilities, and building the right talent to embrace new ways of thinking is critical.
Figure 2. Top Barriers
For example, in Figure 3, I share insights from the research study for the Supply Chain Insights Global Summit on embracing new forms of analytics. Embracing these new forms of analytics requires learning a new language and working with technology companies that most supply chain leaders do not know today.
Figure 3. Analytics Techniques for Supply Chain 2030
Culturally, companies need to bridge the difference between a traditional focus on continuous improvement and the need to drive a disruption. For example the shift from inside-out to outside-in processes is a disruption. It cannot be tackled as an evolution. Digital manufacturing is also a disruption. It is not an evolution. To drive improvement in balance sheet and income statement performance, get clear on what is disruptive and when to focus on as continuous improvement.
The movement from functional excellence to cross-functional work processes supported by a balanced scorecard is a major change transformation. Hit it head-on through continuous improvement work in horizontal processes like revenue management, sales and operations planning, supplier development, social responsibility and new product launch integration. Communicate the balanced scorecard for the team through clear leadership communication and stay the course. Pick five to seven balanced metrics and hold all functions accountable to these corporate metrics.
As you work on your strategic plans for 2017, use Figure 4 as a guide to ask your organization tough questions. Are you building next generation supply chain talent? Can you organization adequately discuss how you are going to build 2030 strategies? Is there a clear design? Are you clear on the role of analytics, robotics, and the Internet of Things? What does machine-to-machine automation mean for your supply chain? Do your work teams have a clear vision of the skill sets required for the autonomous supply chain? Do you know what the network of networks looks like for your team as a goal? Or are they hampered by a lack of knowledge on how to speak a new language to embrace open source analytics, and rethink the current limitations of Enterprise Resource Planning (ERP) architectures and the constraints of master data management? Is there a need to retool? Learn a new language? And better define the supply chain that could be while identifying what this means for job progression, work teams and change management? Based on the research in Figure 4, I think that this is the work that lies before us.
I strongly believe that conventional training on historic functional processes is not sufficient. Driving the future requires innovation.
Figure 4. Current State of Talent
Next week, in Arizona, 120 supply chain leaders will be meeting to network on the Future of Supply Chain 2030. They, as a group, will imagine together a future state for 2030 based on presentations from thought leaders. The event will be live streamed globally to an audience of over 5000 supply chain professionals, and we will be taking questions from twitter through the hashtag #imagine2030. We hope to see you on the live stream. We firmly believe that supply chain talent is the missing link for the future of Supply Chain 2030 and we want to help supply chain leaders drive competitive advantage. This week, please join me in raising a glass to supply chain leaders everywhere. Together, let’s tackle building new capabilities!
I know with travel budgets and work conflicts that not everyone could attend the Supply Chain Insights Global Summit. To help, we share all of the research and the videos from the event. Here is the video on Building Global Supply Chain Talent from the Supply Chain Insights Global Summit. Listen as Jose Luis Deya, Latin America, Syngenta; Walaa Maher, GCC Supply Chain Director from Kimberly-Clark, and Mourad Tamoud, SVP from China Schneider Electric share their thoughts on the research. Join this event through the videos and let us know your thoughts. I look forward to hearing from you! We hope that you can make the event live next year….
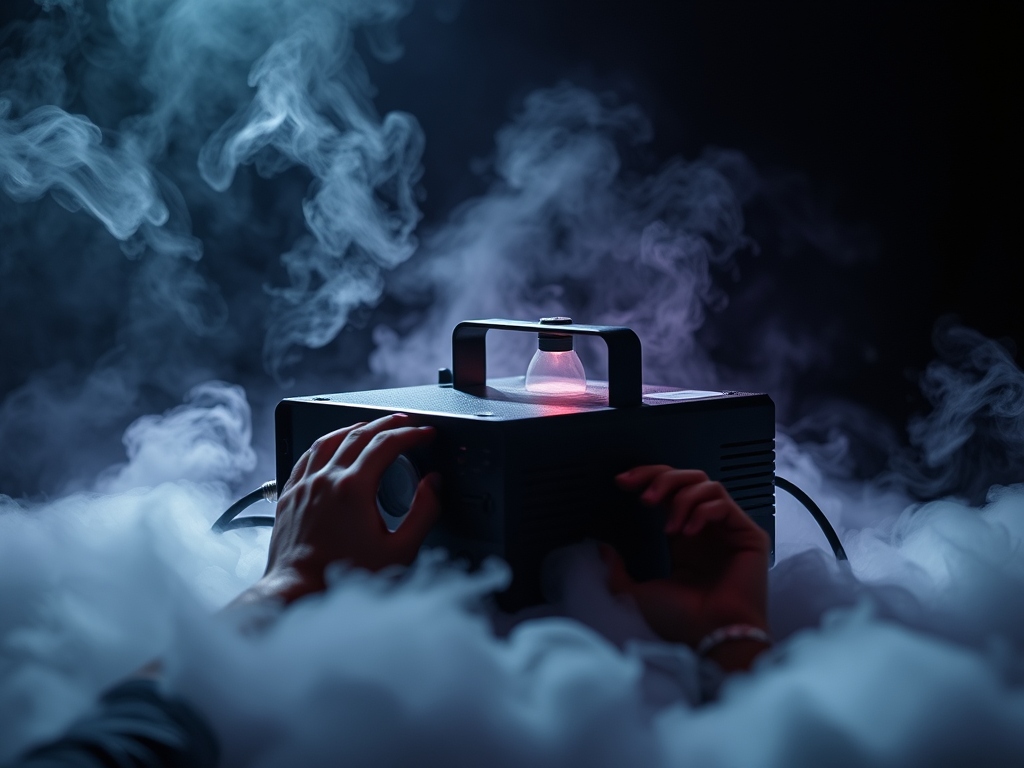
Turn Off the Fog Machine: Move Past Groupthink to Drive A Positive, Data-Driven Narrative
In this blog post, Lora Cecere, Founder of Supply Chain Insights, asks if our current focus on doom and gloom is a fog machine, and a barrier to driving improvement.