Investments come in waves. In my lifetime, I watched business leaders invest in Y2k, eBusiness, Big Data, Social Commerce, and Digital Supply Chains. The net result? Year-over-year, millions of dollars in programmatic spending with questionable value. Now the chase is on for Web 3.0.
Mainly under the guidance of consultants, supply chain leaders try these new concepts in hype cycles. While there is spending in abundance, few question the value. This happens despite the trend of companies being more conservative in their spending. As shown in Figure 1, less than 5% of manufacturing companies are innovators. (Twenty years ago, it was a bell curve with an equal number of late adopters and early adopters. Now it is skewed to more conservative spending.)
Figure 1. Adoption Cycle for Technology
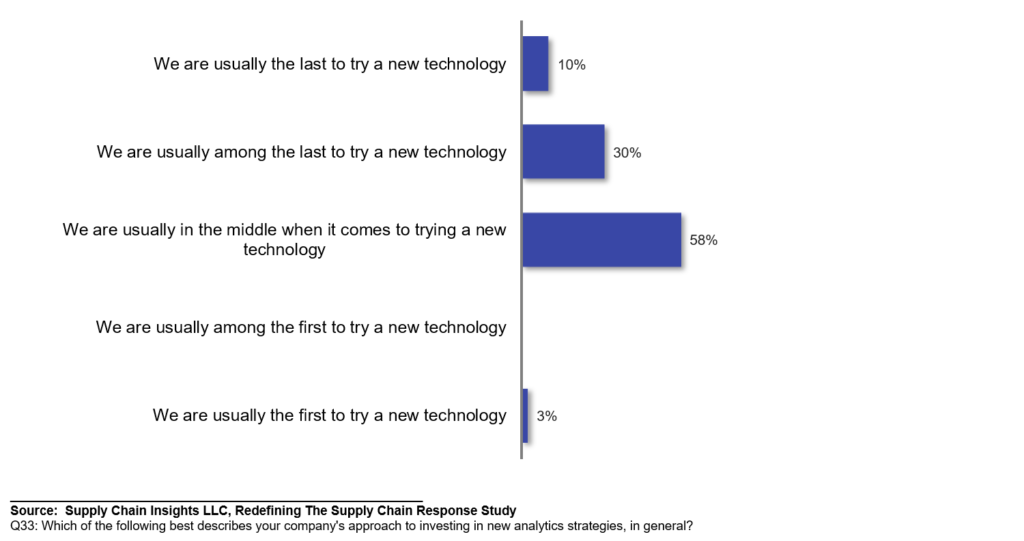
You might say, explain this, Lora. How can this be?
Let me explain. I see the packaging of traditional technologies into new programs by consultants to drive and accelerate spending. While companies are hesitant to adopt new technologies, most have a litany of unfinished IT projects. As a result, traditional technology approaches are bundled into a new wave of spending for the next shiny object.
What Is A Digital Transformation Strategy?
In 2015, the hype cycle of digital transformation began. Today, one in two companies has a digital transformation strategy. What does it mean? When I ask this question in a strategy session, I usually get a blank stare. (One of those looks of, “I wish you had not asked that question.” )
There is no standard definition. The deployments have as many flavors as an ice cream shop. In Figure 2, I list the most common projects from recent research in today’s digital transformation projects.
Figure 2. Current Focus of Digital Transformation Strategies
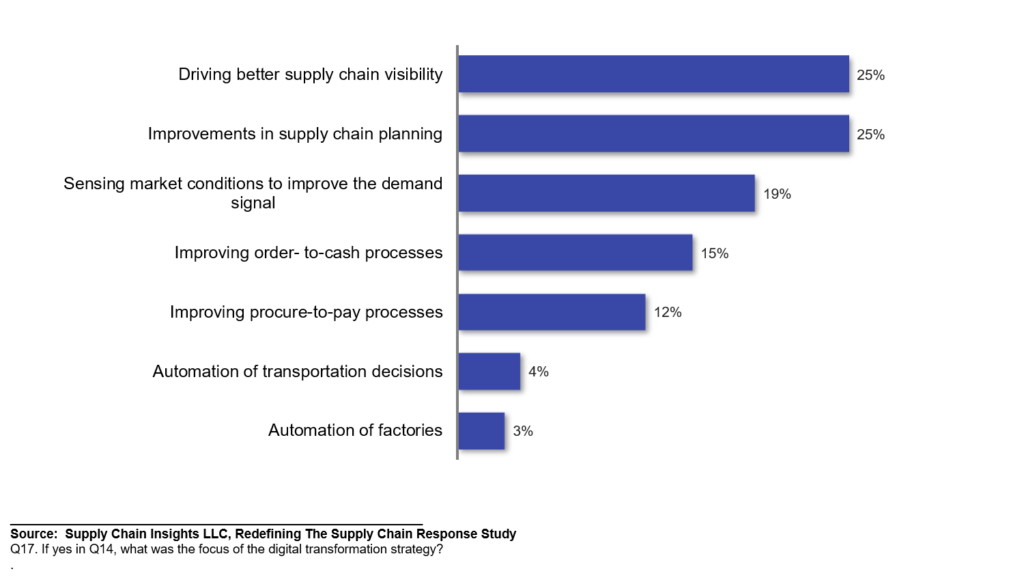
I define digital transformation as the redefinition of the atoms and electrons of the supply chain to improve value. My list includes the redefinition of transportation planning to use real-time data, demanufacturing to reclaim and reduce landfill, redefinition of work, the building of outside-in planning, the building of 3-D printing capabilities, the use of NoSQL to connect real-time data to rules and policy to improve customer-centricity, or the building of value networks to improve track and trace. I struggle to put traditional technologies like ERP, APS, or descriptive analytics under the digital transformation umbrella, but this is what I see. I believe that companies need to test and learn with new approaches to improve value. This is a hard jump for conservative companies.
What Is Successful?
Ironically, while only 3% of companies invest in improving manufacturing–digital twin, hands-free processes, control systems, robotics, and automation–these investments have the highest success rate. As shown in Figure 3, the success rate of supply chain planning and visibility is significantly lower.
Figure 3. Success Rate of Digital Transformation Programs
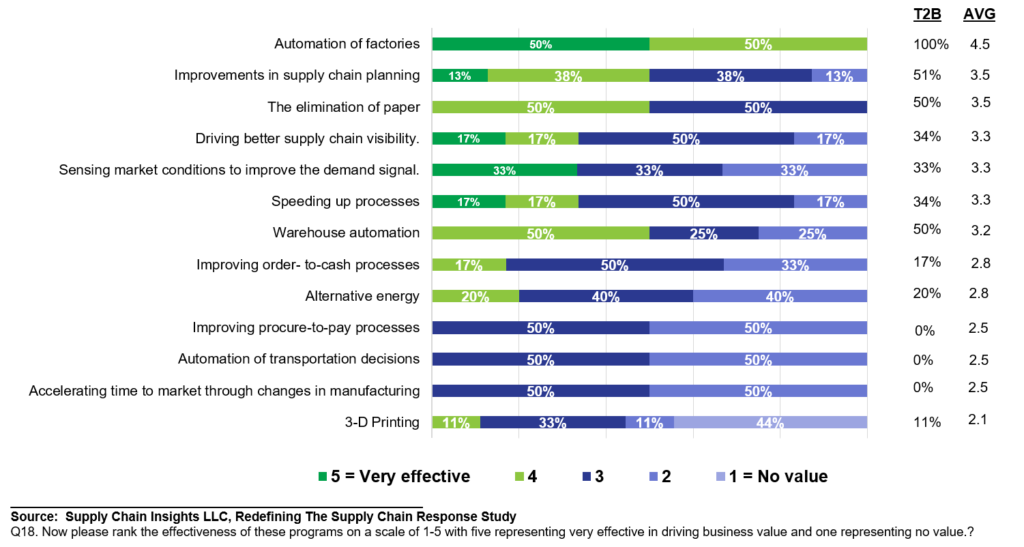
The reason? The most common issue is the lack of clear definitions to guide the scope. Too few companies cut through the hype and cloudy words to make projects executable.
Let me give you an example. Last week, I was asked to speak on building Autonomous Supply Chains. I started by stating a definition. An Autonomous Supply Chain is one where the process operates without human intervention. I then explained that I believed that we were not ready for the autonomous supply chain because most companies are not clear on the definition of supply chain excellence. This prompted the question of does a more agile supply chain improve resilience? I then asked the question of what is agility? How do you drive resilience? Which prompted an intense discussion. Let me explain.
Most companies have 5-7 supply chain flows. Only 9% of companies actively design these flows. The responsive supply chain has short cycle times. In contrast, an efficient supply chain has the lowest cost, and an agile supply chain has the same cost, quality, and customer service, given the level of demand and supply variability. (Usually, a company has 20-30% of the volume that can be managed as an efficient supply chain. However, most companies manage the supply chain as one common flow using the principles of efficiency to guide the process.)
In addition, the new product launch supply chain requires tight integration of business processes with R&D teams and suppliers. The circular supply chain includes returns, demanufacturing, and reclamation. Companies achieve resilience by delivering consistent balance sheet results in the face of demand and supply variability. I could go on and on, but I find the biggest issue to be the grounding on definitions. The second issue is cross-functional collaboration and alignment on what drives value. The third is awareness of data in the company: too few companies use the data that they have.
My point of view? Companies are not ready to build hands-free automation when they are unclear on the design and execution of supply chain flows.
Shiny Objects
This brings me back to the topic of shiny objects. Too few companies are driving the value expected in supply chain planning and visibility projects. My advice? Get clear on definitions and desired outcomes.
I hope this helps.