The story continues. Bloated inventories. Rising inflation. Tightening of organizational belt-cutting to improve cash. Despite investments in planning, today, industries hold 28 more days of inventory than in 2004. Note that in Figure 1, retail home improvements days of inventory increased 68 days, contract manufacturing days increased 48 days, retail apparel by 28 days, and containers and packaging manufacturing companies by 14 days. (The larger the number of days of inventory, the greater the cash drag.)
Figure 1. Changes in Inventory
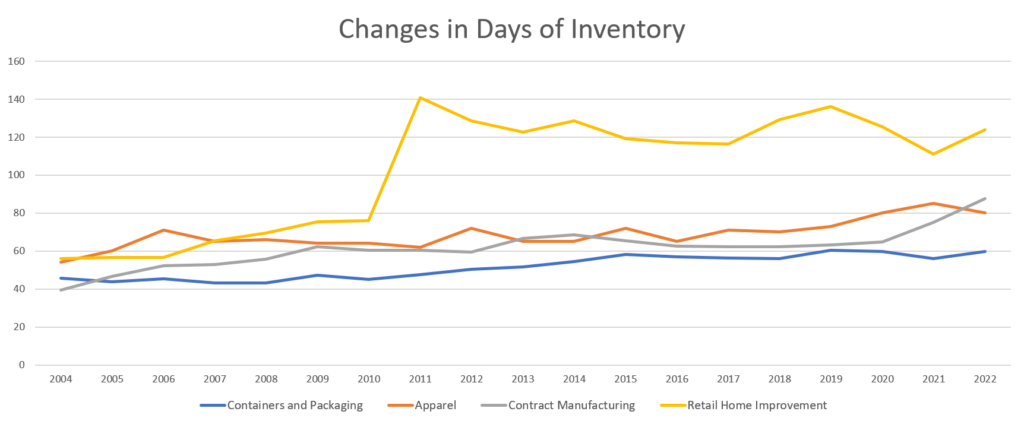
Retrospective
Why do we have issues managing inventory today? The traditional efficiency model, embraced by most organizations as the definition of supply chain excellence, focuses on the reduction of labor costs. The logic is flawed. The minimization of costs within a functional silo, can throw the supply chain out of balance, and increase total costs while increasing slow and obsolete inventory.
Inventory should be owned by the entire organization; however, in most, it is an afterthought. I find that the process of inventory management is not owned by any function or business leader.
In the evolution of the global organization, the issue grew worse. Today’s organization is less aligned than in 2004. The gaps grew three-fold during the last decade. The reason? This is an active area of research. My hypothesis is that there are multiple issues. (For additional insights check out a prior blog.)
Figure 2. Organizational Alignment
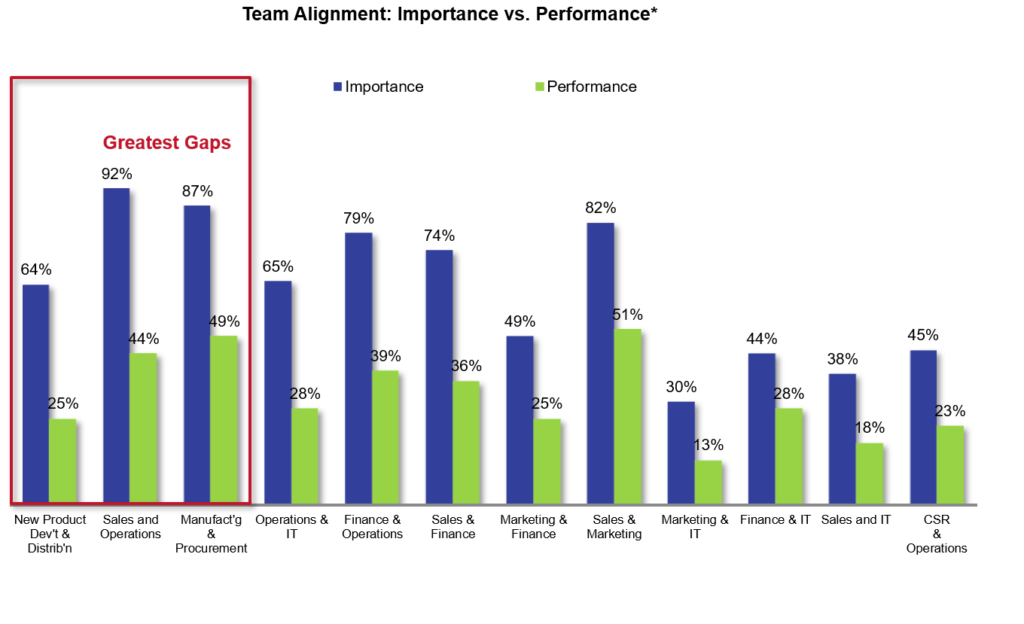
I believe that there are five root issues increasing inventory:
- Decrease in Forecastability. When I work with clients, nine out of ten, have a negative Forecast Value Added (FVA). In the work, I find at least 40% of items have a Coefficient of Variability (COV) greater than .50 making it difficult to forecast with traditional techniques. As a result, a focus only on safety stock is not sufficient. Most companies do not measure FVA and COV to calibrate and adjust their processes. Focus to understand root cause.
- Increase in Product Complexity. The addition of items to the product portfolio increased manufacturing cycle times and increased inventory cycle stock. Over the decade, customer cycle times shorted and supplier response times increased. Many organizations struggle because they have not rebalanced their supply chain cycles and redefined the role of inventory. The opportunity is to manage item complexity and redesign cycles.
- Elongation and Variability of Lead Times. Most decisions to outsource manufacturing are based on a spreadsheet analysis of variable costs without considering the impact of in-transit inventory. The longer the lead-time and the more variable the in-transit time, the greater the impact of inventory on cash flow. Next steps? Analyze the impact of lead time and variability on inventory turns.
- Measurement. Focus on a balanced scorecard to shift from cost to value. Define the role of inventory in your strategy and understand the trade-offs of cost on cash-to-cash.
- A Focus Only on Safety Stock Versus Form and Function of Inventory. Only 9% of companies actively design the supply chain for flow. Without the design of flow, companies cannot define push/pull/decoupling points or define the targets for the form and function of inventory.
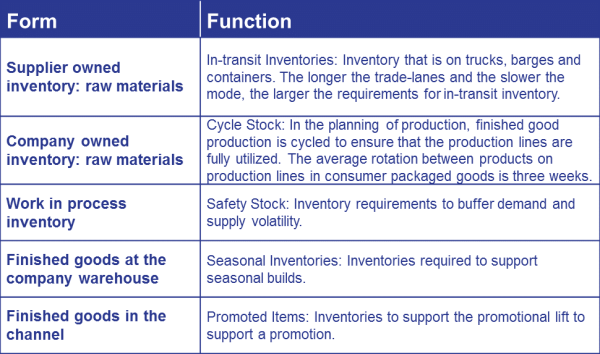
Why It Matters
Cash matters in inflationary times. Today, most companies are sitting on the wrong inventory. The Consumer Price Index (CPI) rose 5.2% year over year in February 2023, following a 5.9% increase in January. This was the largest deceleration in the headline CPI since the rise of inflation in April 2020. The pain level is high, and most companies have the wrong inventory.
The current level of inflation is the highest in two decades. Over the past years, when supply chain volatility and price changes were low, companies implemented IBP with many multi-step meetings and tight integration of the supply chain to the financial budget. This increases process latency (the time to make a decision) and does not help in the defining the right inventory response.
In this time of inflation, managing inventory is paramount. The answer lies in rethinking the fundamentals: design, measurement, and the management of complexity. Traditional supply chain planning approaches are not sufficient. The fix sounds easy, but it is not.
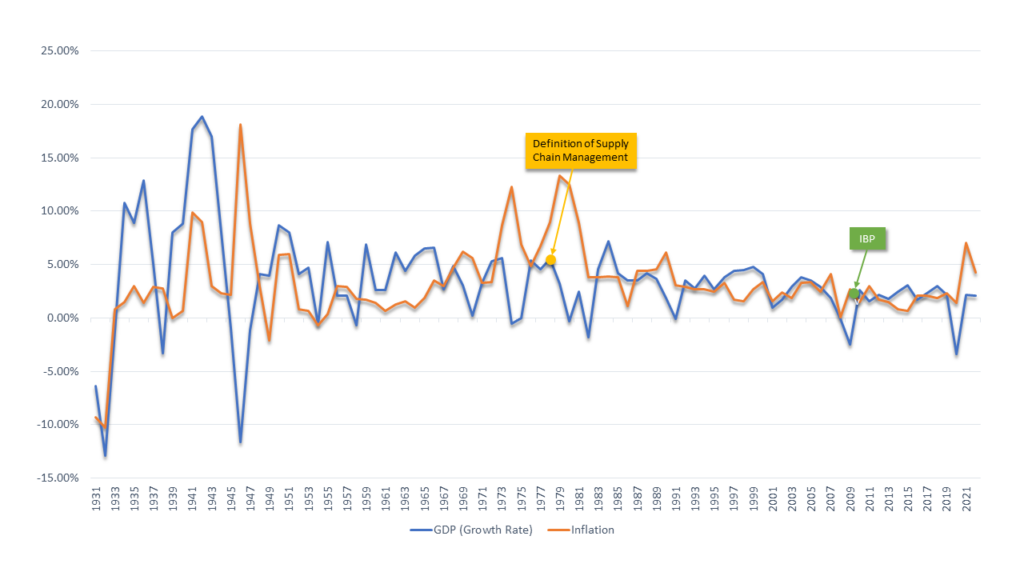
The journey starts with awareness and changing the discussion. I believe that the answer does not lie with real-time inventory (which drives nervousness into the system) or implementing deeper optimization into traditional planning taxonomies. Instead, we need to rethink the fundamentals.
Start by asking, “What is the role of inventory to drive higher levels of value?” The answer is not simple, but the discussion is critical in these inflationary times.
I welcome your thoughts.