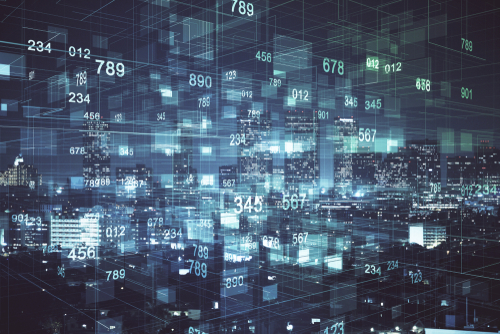
Dear Technologists:
As I worked in my garden and took afternoon naps to recover from surgery for the past month, the content of this open letter circulated in my brain.
In this open letter, I beg you not to layer general AI over conventional supply chain planning. The issue? You might ask, why can what seems to sound so right be so wrong? Why am I so passionate about this? I feel that our current processes are broken, and generative AI has the risk of only helping us to make bad decisions faster. Here I plead for consideration.
My goal? I want to make things better, not worse.
Reflection
I apologize that it has been more than a month since I wrote my last post. My goal is to write weekly, but recently my energy was zapped teaching a class of 90 people the concepts of outside-in planning processes. (I offered the class the week after surgery to see if there would be interest, and within 24 hours, the sign-ups were overwhelming. So, I closed the class. My takeaway? There is interest for us to do something different and improved, but most are searching for the answer of what better looks like.) While new technologies are promising, we have failed to give the market good answers. The current state of supply chain planning, as show in Figure 1, is not sufficient. There is a reason why the most used technology by planners is a spreadsheet.
Figure 1. Current Taxonomy of Supply Chain Planning

I do not want this letter to come off as pedantic or a knee-jerk reaction. My goal is to help. My advice is based on the last year of testing new concepts for supply chain planning, quantitative research, and working with business leaders. I don’t know the answer on how to improve decision support for business leaders to improve supply chain decisions, but I am convinced that if you are honest with yourself, you don’t either. Together, we need to figure out the answer.
I focus on learning from history through research to understand what works and does not and then drive unlearning based on insights. For example, a good way to start the unlearning journey is by understanding why 93% of decisions during the pandemic were made on Excel spreadsheets.
I encourage all my students in my outside-in planning class to keep their “Unlearning Journals.” I have now taught the class on building outside-in processes to over 400 students. In Table 1, I share my unlearning journal.
Table 1. Unlearning Journal Entries From The Class
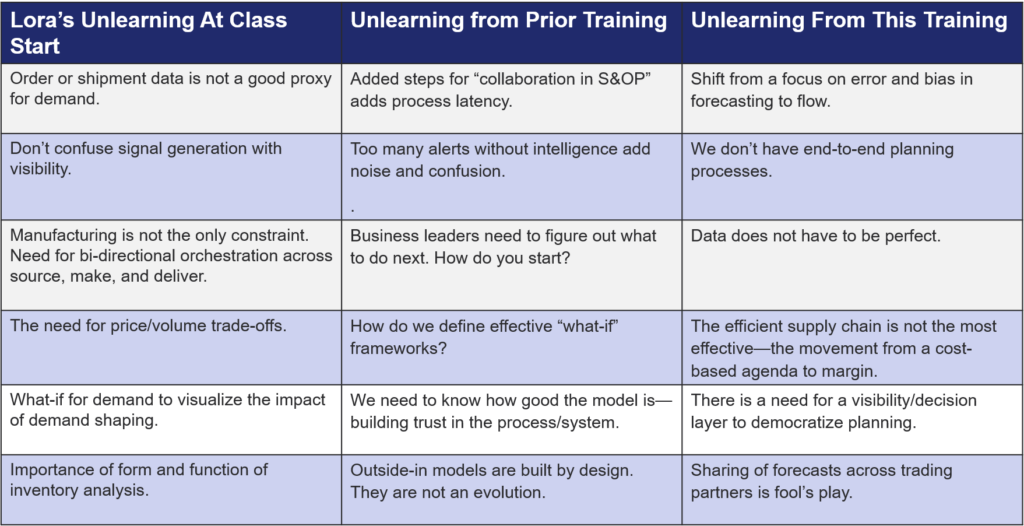
Most companies are caught in the trap of big lies. It is hard to move forward until we admit the issues. The larger the organization, the lies have a greater impact on outcomes. The current taxonomy of supply chain planning was designed for a regional supply chain and was never rethought as companies moved from multi-national to global planning. There are three central to the discussion.
Lie #1. We Have End-to-End Planning. The first is that the current definition of supply chain planning is end-to-end. Let’s have an honest discussion. We do not have end-to-end planning. When we are truthful (often behind closed doors with a beer in hand), we agree that it is not. The focus of today’s architecture is on manufacturing. In the current planning architecture, transportation and procurement operate in isolation. (DRP and TMS have nothing in common. Likewise, revenue management and demand planning outcomes are not aligned. There is nothing in the conventional planning stack to help us improve procurement– aggregate buying or supply execution.) So, let’s face facts. The current definition of supply chain planning is badly flawed. Most technologists talk to me about better engines in a flawed taxonomy. The answer is not a better engine in an old jalopy. We need to rethink the approach. The new solution needs to improve the focus on outcomes. (Did we have a good plan? How well did we accomplish the plan?) No technology today answers these questions. We need to rethink the problem to drive a better solution.
Lie #2. Focus On The Triangle of Trade-offs. The second lie is that supply chain excellence is achieved by trading off cost, customer service, and inventory. The issue? This is an oversimplification. (The larger the organization, the bigger the issue with this simplification. ) The problem? Current solutions only focus on safety stock (usually only 15-25% of total inventory in a global organization), and organizational alignment happens in large organizations when we shift from a focus on cost to growth/margin. (Only 20-30% of supply chain flows can be effectively managed as efficient (lowest cost). The efficient supply chain focused on the lowest cost on low volume and variable products decreases customer service. The only flow that can be managed efficiently is high volume and predictable. And, in this post-pandemic world, we have fewer and fewer products that have a Coefficient of Variability of less than .7. ) The answer lies in the design of the supply chain to recognize and manage distinct flows– efficient (lowest cost less than 30%), responsive (shortest time for a response), and agile supply chain (low volume and highly variable products like samples, new product launch, and channel programs to shape demand).
Lie #3. Functional Optimization Tightly Tied to Enterprise Resource Planning (ERP) Improves Balance Sheet Performance. Many companies believe that the answer is tightly coupled Advanced Planning (APS) to ERP. The problem is that only 20% of data surrounding the supply chain is used, and in a variable world, market data trumps an ERP signal. The other issue is that focusing on functional optimization (inherent in the definition of today’s solution for supply chain planning) throws the supply chain out of balance increasing inventory and total costs. The larger the organization the greater the degradation of performance.
Figure 2. Three Supply Chain Lies We Tell Ourselves
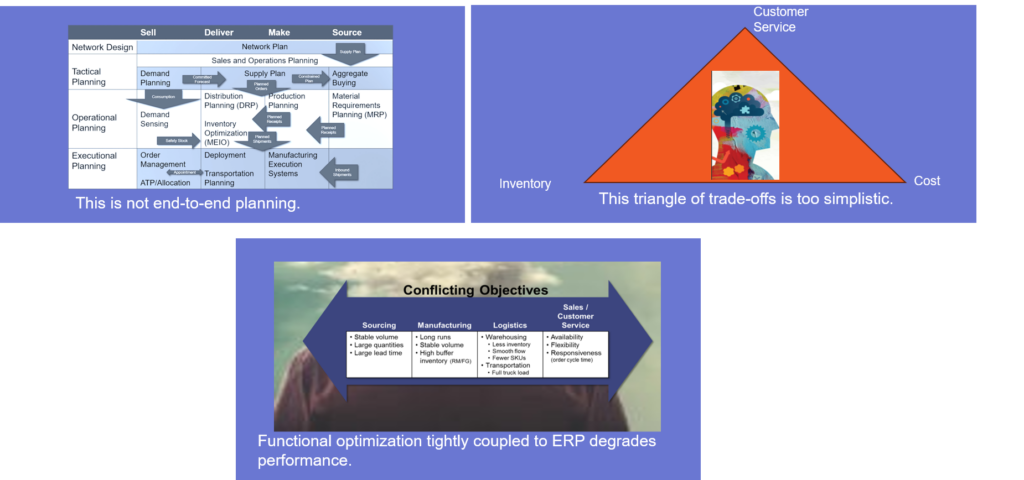
Future Taxonomy of Supply Chain Planning
So, what does the future look like? I don’t know, but I keep drawing images of how planning could change based on the Art of the Possible. My latest thoughts on a potential taxonomy are outlined in Figure 3. In the homework this week, I will challenge the teams of technologists to generate a better taxonomy that is more fitting to drive insights from general and narrow AI.
Figure 3. A Potential Rethinking of Supply Chain Planning Optimization
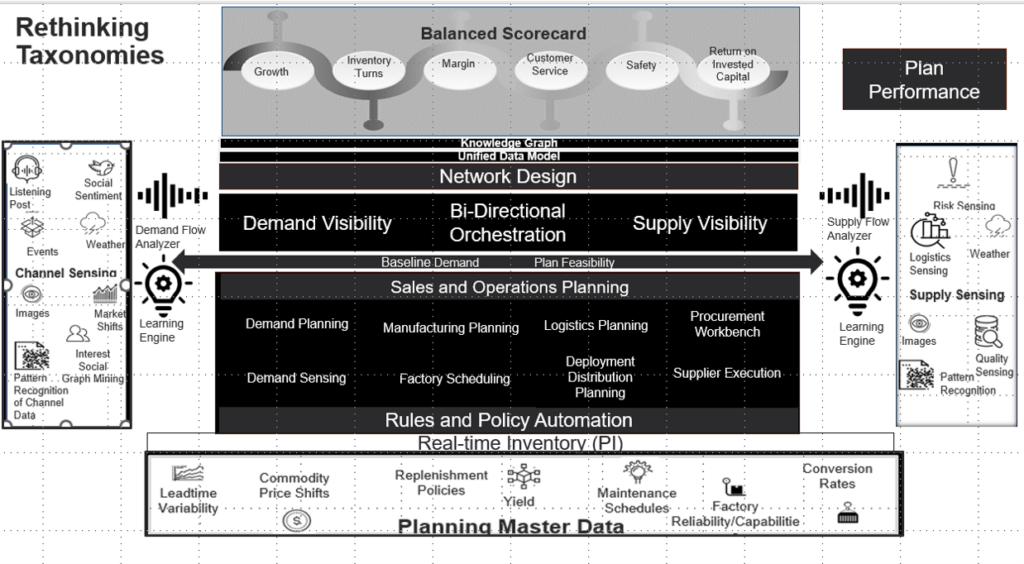
I will be sure to update you, but until then, please do me a favor and not put general AI on top of traditional supply chain planning.
All the best-Lora