Mistakes happen. Supply chain planning user satisfaction is a flip of the coin. Satisfaction is low: one in two supply chain planning software users states satisfaction. Successful implementations start with the software selection.
Supply chain planing is now three decades old. Today over 82% of companies have some form of supply chain planning. With the rash of merger and acquisition activities, many companies have inherited multiple systems. The average is 2 to 3 demand, and 3 to 5 supply chain supply planning solutions operating on 3 to 5 Enterprise Resource Planning (ERP) solutions. There is no one common way to implement planning solutions. Configured by a planning team, based on the business requirement, each planning instance is different. Differences exist in data models, planning hierarchies, and data definitions. As a result it is difficult to roll-up planning data for decision making across the company post-merger. As a result, a search for a new software solution begins.
While many of the technologies have changed and improved capabilities over time, much remains the same. Unfortunately, the decisions for a new solution are often fitful, political debates. The decision cycle will get worse with the evolution of new technologies.
Where to turn? The software integrator is often biased. Why? Many consultants receive commissions on the software sale, and software from ERP providers are longer to implement leading to larger software implementation/consulting revenue for the integrator. What to do? Be aware. In the process, try to seek help from independent sources.
Figure 1. Satisfaction and Implementation Rates of Software Types
As an analyst for over a decade, I am always surprised. Companies looking at supply chain planning software for months, struggle to make a decision. After looking at the software in demos, it is hard for teams to discern differences and rationalize what software attributes are the most important to drive success. In this blog post we offer help by outlining three common mistakes that teams often make in the selection of supply chain planning software.
Fallacy #1: Recognizing the Need for Industry-Specific Functionality
When companies make a decision on supply chain planning, the top criteria, as show in Figure 2, are “ease of integration,” “ease of working with the company,” “financial viability,” and “ease of use.” At the end of the list, and lower perceived, is “industry-specific functionality”. How is this logic flawed?
Integration on a batch basis is not the obstacle in supply chain planing no matter what the decision. (The only exception is the SAP CIF interface for APO. The CIF interface offers improved outcomes between ERP and time-sensitive data like Available-to-Promise (ATP). There is no significant advantage for tactical demand and supply planning.) Batch integration for demand and tactical supply planning is perceived to be a larger obstacle than it is in reality. However, the lack of industry-specific functionality can make or break your project. Having the right data model and collaborative workflows based on industry-specific criteria is one of the most important points to drive value from decision support software.
Figure 2. The Criteria Manufacturing Companies Use to Make Decisions for Supply Chain Planning Software
Industry-specific functionality is more critical in operational and executional planning and less important in strategic design planing. The right data model can make or break a decision for production planning,
Fallacy #2. Not Buying Based on Culture and Willingness to Try to New Technologies
Don’t buy software based on future promises unless you are an innovator. Today there are three times more late adopters than innovators. Only an innovator should buy software in its initial releases. For example, if you are an innovator consider piloting a new software like SAP HANA IBP, Cognitive Learning from Enterra Solutions, or a new release of Oracle for the cloud. If you are not, be wary. Buy in your comfort zone. If you are a late adopter, buy the tried and true. Don’t bet on future promises by software companies. The willingness to try new technologies is outlined in Figure 3. Spend sometime to understand your comfort zone before you contact the technology provider.
Figure 3. Distribution of Innovation in Supply Chain Planning.
Fallacy #3. Tight Integration Is Positive
The best planning implementations are loosely coupled to ERP and other IT systems. Planners need time to plan and they need a planning workbench to enable “What-if” analysis to determine the best plan before passing the plan to an ERP system of record. In addition, master data within ERP is not sufficient for planning. A requirement for success is attention to planning master data. Define it and refine the requirements continuously based on planning parameters.
The most successful supply chain planning systems will embrace data strategies holistically. What does this look like? Staged and cleansed prior to ingestion by the planing engines, planning master data is critical to success. In addition, a planning workbench with what-if analysis to derive the best plans drives better results. Based on our research we estimate that this is only 32% of implementations.
When we study companies who believe their supply chains are working well, there are several commonalities. We show these in Figure 4. Significant at a 90% confidence level, companies that are good at planning are also good at data management. Data strategies are holistic. In these organizations there is a clear understanding that managing planning inputs is critical, that data models need continuous fine-tuning, and outputs tested for validity and purpose.
Figure 4. Characteristics of Companies “Working Well”
We hope this helps. Please let us know if you have any questions.
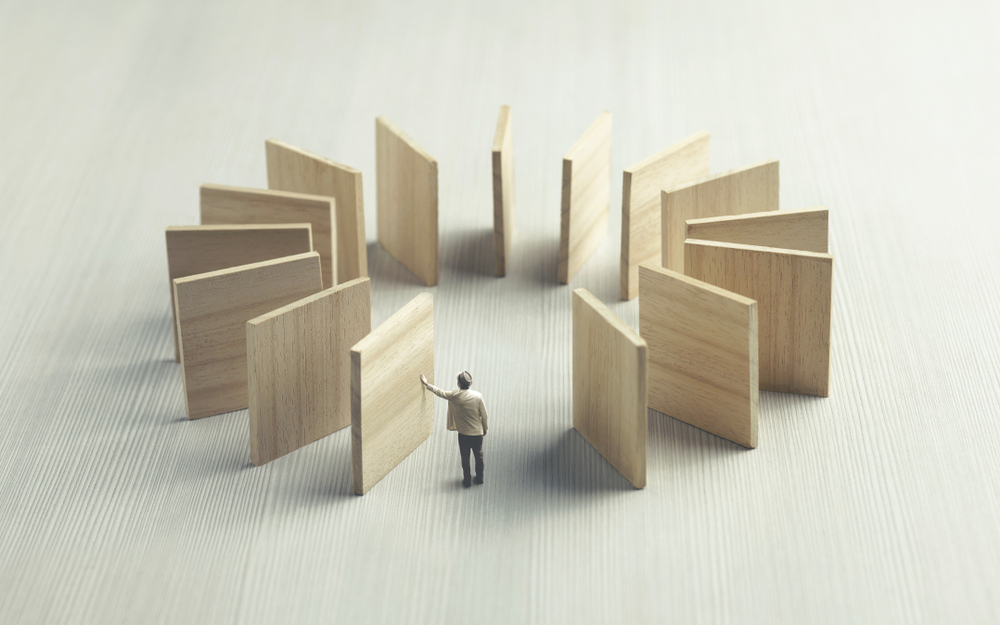
Please Don’t AI Stupid
Drip. Drip. Drip. Industry 4.0. DripBig Data. Drip.The Connected Supply Chain. DripDigital Supply Chain. Drip.Autonomous Supply Chain Planning. Drip. Self-Healing Supply Chains. Drip. Touchless Supply