I am writing this blog post in the air, sitting in seat 4c, somewhere over the Midwest en route to Philadelphia. As I look below, I see field after field of United States farmland. The land looks like a giant puzzle. After a busy week with high-tech and electronics clients, my fingers are itching to help others solve a different type of puzzle. The goal of this blog is to help business users maximize their current SAP Investments in a time of change.
Reflections
High-tech manufacturers in the Silicon Valley of the United States are some of the best at supply chain planning. With changing product profiles, short life cycles, constraints with downstream suppliers, and changing markets, being good at supply chain planning matters. In this tough market excellence in supply chain planning is a critical element to be competitive. In high-tech, supply chain planning is more important than in other industries like chemical, pharmaceutical, consumer packaged goods and retail.
Over the course of the last decade many clients implemented supply chain planning but have struggled to maximize the value. The reasons are numerous. Planner turnover, time to plan, ability to get to data, system usability, and talent gaps are all major issues. Getting good at planning requires executive leadership. Business leaders need to support a new way of doing business. It requires investing in planning talent, and the recognition of planning as a core competency. Most companies fail before they succeed.
Getting good at supply chain planning also requires the adoption of a different cultural paradigm. How so? Most organizations reward the urgent. The urgent gets in the way of the important. Planning is important, and planners need time to plan. When companies reward fire fighting, they never get good at planning. Supply chain planning and the discipline and rigor is a different way of working. To get good at planning, it requires focus and discipline.
At Supply Chain Insights, we complete 25-30 quantitative studies a year. Most of our work is focused on supply chain planning. The respondents vary by study; but during a year, we will collect about 3,000 unique responses. In the research I notice three trends:
1) Demand Planning Is Stronger than Supply. We have made more progress in forecasting than supply planning. Organizations are happier with their systems in the areas of demand planning than supply. Demand planning processes are less industry-specific and the principles can be more widely applied than those of supply planning. Satisfaction with supply is much lower. Constraint-based modeling and “what-if” analysis are major gaps.
2) Increased Dependency on Excel Spreadsheets. Despite large investments in supply chain planning, today, the global multinational is more dependent on Excel. Due to usability issues, Excel is the planning system of choice. While companies have deployed large planning systems, Excel ghettos have popped up in most organizations. Planners plan in Excel and write the results to the supply chain planning system. The gap has grown. Most organizations struggle to use the planning technologies. Few realize that they will never be able to model the complex, non-linear supply chain relationships in an Excel spreadsheet.
3) Business requirements Are Changing. Forecastability (the ability to forecast a product line) has gotten worse, demand error and bias is increasing, and supply is more complex. The rhythms and cycles of business have increased. Organizations want better decisions faster. As a result, organizations struggle to match the cadence of planning to the required cadence of the business.
So, bottom line, most organizations are looking to improve their supply chain planning systems; but at the core of this discussion with my clients that have chosen SAP supply chain planning technologies, the question is, “What should we do with our supply chain planning systems from SAP?” While the name of SAP’s Supply Chain Planning suite has changed to SCM7 (the old name was SAP APO), the gaps are glaring.
I council clients to stabilize their investments in the SAP Supply Chain Planning technologies, and recognize SAP APO with the CIF Interface as a planning system of record. For SAP users, it is the best and a much needed system of record. Why a planning system of record? Most organizations have 2-3 demand and supply instances and 5-7 ERP systems. The IT world of a large multi-national is complex.
I then recommend that the business augment the SAP SCM functionality using best-of-breed, industry-specific optimization. I recommend using best-of-breed solutions to write to the current SAP APO framework. Here is my advice.
Why I Believe SAP SCM Is a Risk to Your Business.
In these sessions I always encounter a discussion around IT standardization. Most business users must justify to their IT teams that they need to justify doing something other than SAP supply chain planning. This article is written to help organizations better address this question.
In many companies, SAP has a lock on the decision processes. The SAP team is masterful at selling the value of SAP everywhere to the C-suite, and the system integrators, with deep bench strength in SAP, will nod in agreement. (The dirty little secret is that the system integrators make more revenue and profit on SAP deployments than other planning options. So, it is in their best interest to support the implementation of SAP Supply Chain Planning software.)
For the record, let me state a few facts that I strongly believe. SAP is one of the best, if not the best software vendor, at writing software code when they are clear on the requirements. The SAP solution is better than the Oracle SCM solution for planning. The problem is that supply chain planning is just not a hot market for SAP to invest in, and the culture struggles to attract and retain thought leaders.
I also believe that SAP is one of the best, if not the best, ERP system for most process manufacturers. So, why do I not believe in SAP SCM 7? Why am I so bold as to pen an article to state that the investment in SAP SCM 7, and the migration from SAP APO, is a risk to your business? I have three primary reasons. It is centered in the now, the ten-year vision, and the opportunity.
1) SAP Supply Chain Planning Is a Poor Supply Chain Planning and Optimization Technology. Let’s face facts. When SAP launched APO in 2002, the optimization technologies were inferior to most best-of-breed technologies in the market. Over the years, as technology innovation has improved, staying current on supply chain planning optimization has not been a focus for SAP. Relative to other technology development areas, the opportunity for SAP was not as great. They quickly became a market leader, and then shifted resources to other areas.
As a result, the most successful SAP Supply Chain Planning implementations layer on optimization technology from a specialist vendor or University. It is an expensive workaround.
In addition, the SAP Supply Chain Planning solution is more expensive, has a longer time to value, and is harder to use than alternative solutions. In a study of 187 supply chain planning instances, we found a correlation at a 90% confidence level that SAP APO implementations were longer to implement, lower ROI and user satisfaction than best-of-breed technologies from JDA, Kinaxis, Logility, or OM Partners.
The data from this study is shown in Figure 1. While consultants will often rationalize the difference away stating that an 80% fit is good enough, the wise business leader knows that supply chain planning is not a game of horseshoes. Model fit and speed are essential to plan. The SAP Supply Chain Planning suite of products is not competitive. This is especially true for the core business user/planner.
Figure 1. Relative Comparison of Best-of-Breed Providers versus ERP Expansionists like SAP/Oracle
2) SAP Is Discontinuing Support of the Current Supply Chain Planning Technologies. At first the announcement by SAP was that SAP APO would be discontinued in 2020. Following a customer uproar the date was extended until 2025. Assuming that it takes 3-5 years to build an effective planning organization in a global multinational, the rewriting of the SAP Supply Chain Planning platform is an opportunity cost to the business implementing the solution. It is not an evolution. Instead, it is a re-implementation. While SAP is busy redefining the architecture, a reimplementation has risks.
This movement from SAP APO to SCM 7 is a redesign of supply chain planning by SAP. It bundles Integrated Business Planning, a Supply Chain Control Tower, Inventory and Demand/Supply planning into a new cloud-based architecture based on HANA. The solution is evolving, and will take time. In my calls I find that current references report significant issues—roll-up and roll-down of hierarchies, and depth of demand functionality. They are actively partnering with SAP to make the new architecture work. They will get there, but the progress is slow. Mature SAP manufacturing IT and line-of-business teams have been testing the functionality for more than a year and currently do not consider it mature enough for rollout. Consideration of the new technologies is currently recommended by only mature SAP/line-of-business teams used to working through implementation issues with SAP.
The rewrite extends to redefining ECC architectures. Current functionality of SAP GATP and SAP APO PPDS (production planning) will be moved into the ECC ERP frameworks. Since most companies have 5-7 ERP instances, this approach will fragment the functionality slowing the implementations and making it more difficult to build multitier ATP and visibility solutions. Multitier optimization is critical for optimizing the outsourced network.
SAP SNC will be moved into the Ariba Network. SAP is pushing for the adoption of the Ariba network for B2B connectivity and inter-enterprise business process management. The adoption rate is slow. Ariba, while mature for indirect procurement, is still not the preferred method for direct material management.
I wish the SAP team luck in this endeavor. If history is our guide, competitors’ rate of success of re-platforming a supply chain planning solution is low. I know of no time in the history of supply chain planning where a rewrite of the supply chain planning platform has been successful. The launch of Manugistics 7.1/7.2 was a failure, and was a nail in the coffin for a struggling supply chain planning vendor 15 years ago. In parallel, the rewrite of the Numetrix software by Oracle was also problematic. History shows that a major rewrite of supply chain planning platform will take five to six years to stabilize. So, while the shift in adoption will happen in 7-10 years, the issues with bugs and bug-fixes will take much longer.
The new redefinition of the SAP architecture is a better fit for casual users than for core planners. With the increase in business constraints and the complexities in demand, companies that are good at planning will need to focus on the systems for core planners first, and then augment for casual users. The design of the new SAP solution is a better fit for the casual user than the core business planner. If I were a SAP line-of-business user, I would use this time to find a better planning solution than SAP APO or the promise of SCM 7.0.
Figure 2. Supply Chain Planner Continuum
3) Opportunity Cost. Supply Chain Planning is moving in new and exciting directions. The redeployment of SAP SCM is an opportunity cost for SAP to take advantage of this innovation.
We are entering into a period of rapid change for planning and the redefinition of supply chain planning architectures. Concurrent optimization, unstructured text mining, streaming data and sensing, and cognitive learning are converging. I believe that these forms of innovation will redefine supply chain planning into learning systems within five years. What does this mean? Using cognitive learning, our supply chain planning solutions will think and resolve exceptions as we sleep. Sensing through pattern recognition and sensors will shorten cycles for response. This will transform planning, making the system less reliant on manual data touches and the traditional business planner. This technology advancement will happen concurrently with the relaunch of the new SAP Supply Chain Planning Software. As a result, I believe that SAP innovation will lag and SAP will play catch-up in 2025. Investment in the SAP rewrite is an opportunity cost for the average business user to embrace new and more promising technologies.
The second area of rapid change is the use of canonical B2B operating networks to improve B2B flows. As this happens, we will see multitier Available to Promise (ATP) solutions, online network performance benchmarking, and much more advanced multitier sensing and modeling. SAP is an enterprise system. It is not a one-to-many or a many-to-many data model. The movement of significant pieces of SAP planning into ECC architectures will make it more difficult to move to support multitier functionality.
What to Do? Steps to Take…
So, if you are in an SAP shop with an SAP dictate, socialize this blog post. I think that blindly following the SAP-only path for supply chain planning is a major risk to the business. At the end of the debate, let me know your thoughts. If you believe that I am wrong, I will re-write this post. I know that this is a contentious and political debate in most organizations, but, I think that it is a discussion that needs an open forum in the industry.
As the debate ensues, what do I recommend?
1) Stabilize your SAP investments. Implement the SAP supply chain planning systems as a system of record. Use the SAP APO solution with the CIF interface without the optimization engines as a system of record. Write to the SAP planning system of record from best-of-breed solutions for optimization and cognitive learning.
2) Use in-memory visualization tools to drive insights from data. Don’t limit yourself to the SAP BI technologies. Invest heavily in visualization technologies like Qlik, Tableau, and Spotfilre to drive value and insights.
3) Invest in technologies that can model your business and that your planners will use. Supply chain planning is very industry specific and 80% is not enough. Spend time testing and refining the planning systems.
4) Actively follow the SAP rewrite and redeployment of the SAP SCM 7. Stay involved, but watch from the sidelines. If there are pieces of this solution that interest you, be a late follower. Let others work out the issues.
5) Stay connected in the industry. In the evolution of the industry, trust but verify. Actively network with SAP users and watch the deployments. Sidestep the hype and marketing rhetoric, and stay focused on the delivery of real business results.
These are my thoughts. I would love to hear from you!
____________________
Life is busy at Supply Chain Insights. We are working on the completion of our new game—SCI Impact!—for the public training in Philadelphia in August and the content for the Supply Chain Insights Global Summit in September. Our goal is to help supply chain visionaries, around the world, break the mold and drive higher levels of improvement. The conference will feature case studies on demand sensing, rules-based ontologies, and the use of sentiment analysis.
About the Author:
Lora Cecere is the Founder of Supply Chain Insights. She is trying to redefine the industry analyst model to make it friendlier and more useful for supply chain leaders. Lora has written the books Supply Chain Metrics That Matter and Bricks Matter, and is currently working on her third book, Leadership Matters. She also actively blogs on her Supply Chain Insights website, at the Supply Chain Shaman blog, and for Forbes. When not writing or running her company, Lora is training for a triathlon, taking classes for her DBA degree in research, knitting and quilting for her new granddaughter, and doing tendu (s) and Dégagé (s) to dome her feet for pointe work at the ballet barre. Lora thinks that we are never too old to learn or to push the organization harder to drive excellence.
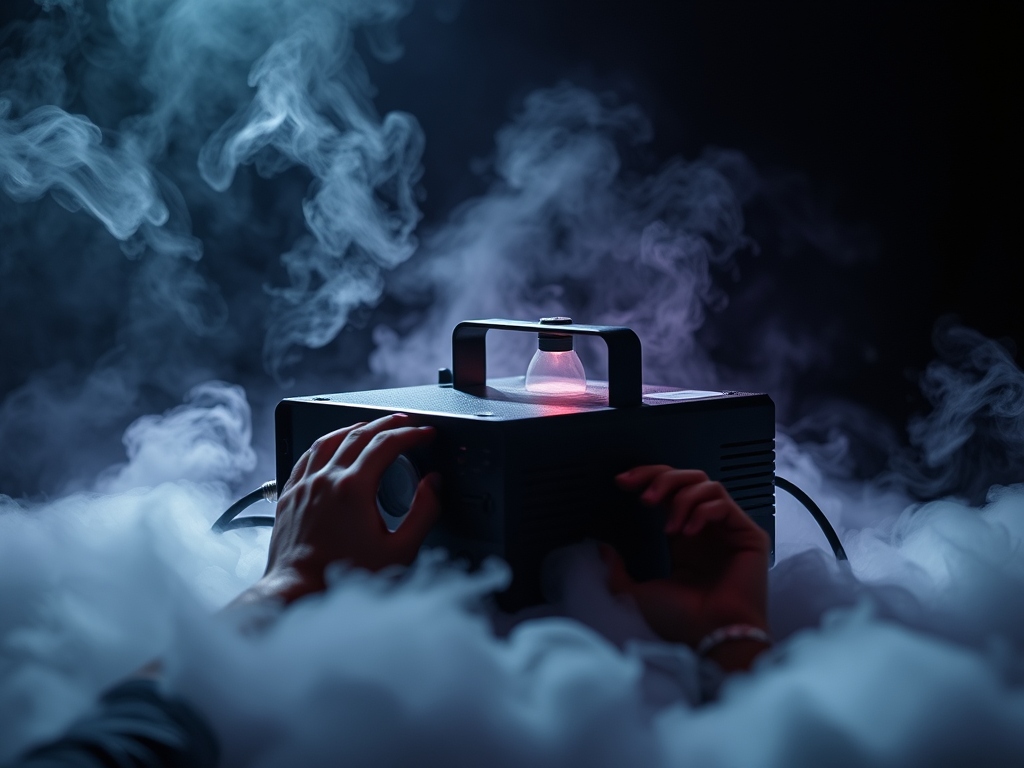
Turn Off the Fog Machine: Move Past Groupthink to Drive A Positive, Data-Driven Narrative
In this blog post, Lora Cecere, Founder of Supply Chain Insights, asks if our current focus on doom and gloom is a fog machine, and a barrier to driving improvement.