Paradox: A statement or proposition that, despite sound (or apparently sound) reasoning from acceptable premises, leads to a conclusion that seems senseless, logically unacceptable, or self-contradictory. Definition
Anomaly: something that deviates from what is standard, normal, or expected. Definition
As I follow the evolution of supply chain technology, I am struck by what I see as a stream of paradox and anomaly, and the tendency of supply chain leaders to cling to convention. I constantly ask myself, why? Why? Why?
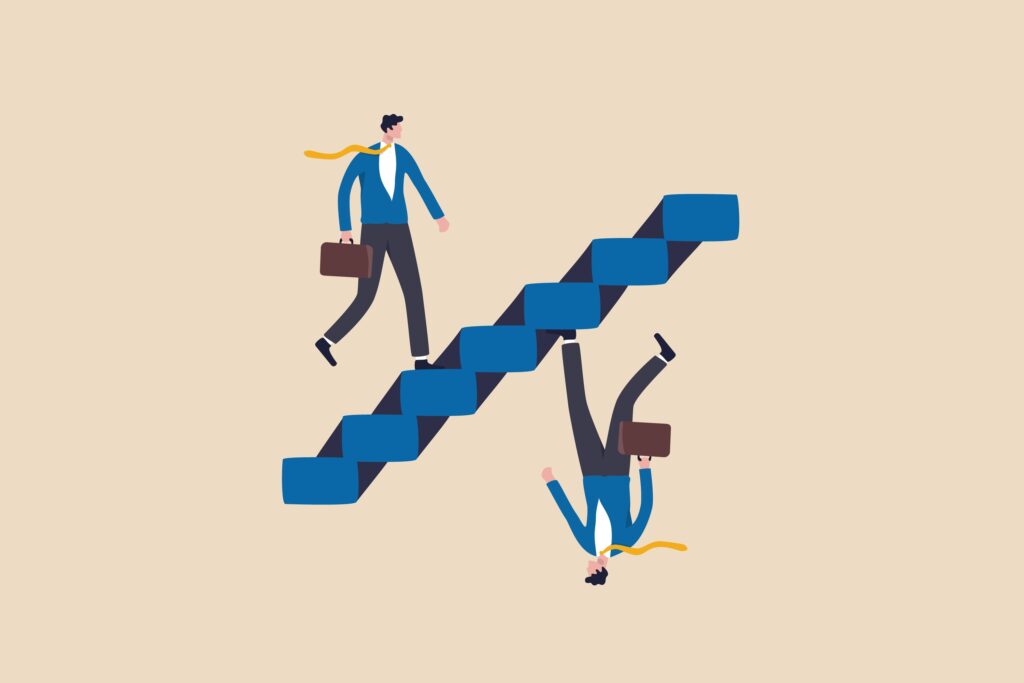
Maybe I am old, tired, and cranky. Or tired from two weeks of road travel… But after twenty years as an industry analyst in supply chain technology, I struggle with why we cannot make more progress in the adoption of technology to make better decisions. Let’s explore nine in this blog.
- Art of the Possible. Today’s supply chain leaders have a fascination with Artificial Intelligence (AI) but are blind to the advantages and capabilities of Web 2.0 technologies. Companies have data lakes, but do not use their own data. I don’t understand why companies want to move data in and out of data jails that we call relational databases but are so unaware of the techniques to use data from data lakes through schema on read technology approaches. The world of NoSQL unified data models is inconceivable to most.
- Transition from Transactional Thinking to Flow. Software built on graph technology can model flow, but the transactional paradigms of historic practices hold development team’s hostage. I am excited by the graph, but disappointed in the industry’s use of the graph to drive process improvement. My observation is that software technology leaders are attempting to make historic practices faster versus redefining capabilities. Leaders in building supply chain capabilities on graph technologies are failing to drive break through process innovation.
- Building the Effective Global Supply Chain. We speak about the need to move from a functional understanding to a global, holistic capabilities, but the traditional supply chain leader defines bonus incentives and process performance goals based on functional metrics. The larger the global corporation, the more that the use of functional goals sub-optimizes growth, margin and inventory levels.
- Measurement. Organizations speak of the bullwhip, but don’t measure it or monitor the effects. Many companies claim goals for net zero, but there is no investment in networks (where 70% of the exposure lies) and the impact is not measured. If these goals were important (which I believe that they are), why would we not measure progress and impact?
- Bi-Directional Flow and Value Networks. Every supply chain leader understands that effective processing in the supply chain requires bi-directional flow and network automation. Yet, the primary investment in supply chain systems is linear with a focus on enterprise efficiency. With the low investment in network technologies and the slowing of innovation, the primary networks are being desecrated by private equity firms. Innovation is slowing. Or by enterprise solutions to sell more of traditional wares. No network provider is driving interoperability between networks or break through thinking in outside-in processes.
- Innovation. In 2004, my research showed a bell curve of innovators and laggards. Today, it is a skewed distribution with only 7% of manufacturing and retailers claiming to be innovators to drive first-mover advantage through technology. The continual drone of badly written RFPs is an opportunity cost for the market. Never in my lifetime as an analyst has innovation been so promising, yet so mis-understood and not utilized.
- Time. The industry is drowning in real-time data, but yet, process latency in S&OP increased 80-90% in the past two decades. Unknowing consultants layered meetings after meetings after meetings onto regional supply chain processes adding 50-60% latency to the output of decision support technologies.
- Attempting to Get Perfect on Imperfect Data. I often laugh when companies ask me to define a good forecast. For me, a good forecast has zero demand latency, minimal bullwhip effect, little bias, and improvement in Forecast Value Added (FVA) analysis. Few companies that I work with are familiar with these terms. Instead, they are attempting to measure demand forecast error and lamenting the lack of perfection on imperfect demand data. Working in the area of demand management, requires the building of an organization that can work well in the world of gray where good is not black and white.
- Engines, Models and Workflow. Most of the discussions in supply chain planning center on better engines. We are not questioning the fit of models and the tie to workflow. In selection, we are not testing outcomes. An engine without a chassis does not get us very far.
Join Me: Do a Flip Turn
I am a swimmer. Three times a week, I grit my teeth and push off the wall at the local pool. At first the water is cold, and I resist submersing my face. But, as I push off the first wall, I start the familiar cadence of lap after lap. My mind will then start to transcend the motion of the body in an elevated state. I think clearer. When I finish the last flip turn, life is better.
My request. Please don’t fall prey to the pretty PowerPoints, conventional case studies, magic quadrants (that have no magic), and the multiplicity of hype cycles. Push off the wall and relish the breath of fresh air at the end of the flip turn. Supply chain excellence is about people doing powerful things with atoms and electrons to improve economies and lives. Don’t fall prey to programs of the month like digital transformation.
As you read through the barriers paradoxes and think through the anomalies of today’s supply chain practices, please join me in questioning today’s supply chain practices. Not for what they are, but for the enormous opportunity cost of what they could become. I strongly believe that we need to redefine work to improve insights. The greatest paradox of all is that in the face of unprecedented demand and supply variability in the pandemic, 93% of decisions were made on spreadsheets. The millions of dollars invested in ERP/APS were not sufficient.